Este manual de instruções destina-se a ser um guia para a utilização da prensa RFlex . Para garantir o melhor desempenho da sua máquina de soldar, siga rigorosamente as recomendações e especificações.
Índice
- Capítulo 1: Utilização prevista
- Capítulo 2: Sinais de segurança e pictogramas
- Capítulo 3: Dados técnicos
- Capítulo 4: Descrição técnica
- Capítulo 5: Montagem e instalação
- Capítulo 6: Funcionamento
- Capítulo 7: Seleção dos parâmetros de soldadura
- Capítulo 8: Manutenção
- Capítulo 9:
Saúde e segurança no trabalho
- Capítulo 10: Documentação eléctrica
- Capítulo 11: Documentação pneumática
- Capítulo 12: Instruções gerais
- Capítulo 13: Apêndices
- Capítulo 14: Documentos adicionais da máquina
Para obter mais informações técnicas sobre esta máquina, contacte o nosso Centro de Resolução através do número 1-855-888-WELD ou envie um e-mail para service@weldmaster.com.
1.0 Visão geral da máquina/utilização pretendida
A prensa RFlex é a máquina mais pequena da nossa linha de máquinas de radiofrequência. Tem uma construção robusta e foi concebida para garantir precisão e uma longa vida útil e possui uma corrediça de montagem com cabeça de aço muito robusta, formada por um mecanismo de duplo "V".
Para trabalhos de "costura", recomenda-se um pequeno suporte de ferramenta para dar boa visibilidade e acesso à área de trabalho. Para outras aplicações, pode ser fornecido um suporte de grandes dimensões que proporciona um apoio rígido numa área de ferramentas ampla. Também estão disponíveis instalações para aumentar o espaço da garganta, onde os materiais em excesso têm de ser posicionados atrás das ferramentas.
A máquina é amplamente utilizada nas indústrias médica, automóvel e de vestuário para soldar pequenas peças adicionais, como tubos, válvulas de ar e fluidos, ganchos, ilhós, placas, etc. RFlex A prensa tem uma potência HF de 0,5 a 4 kW. A máquina é a ferramenta perfeita para a produção auxiliar onde a precisão, a acessibilidade manual, a durabilidade e a resistência são fundamentais. Miller Weldmaster coloca sempre a qualidade, a precisão, a eficiência, a segurança e a simplicidade do design em primeiro lugar.
AS CARACTERÍSTICAS MAIS IMPORTANTES DA MÁQUINA:
- a manutenção de rotina da máquina é muito simples;
- a prensagem pode ser ajustada com precisão;
- o fabricante instalou o botão de emergência no painel de controlo;
- a máquina está equipada com a coluna de luz de sinalização para aumentar a segurança do operador quando a máquina está ligada;
- o operador pode programar e controlar o ciclo de trabalho da máquina graças ao painel sensível ao toque HMI;
- a ferramenta de programação permite ao operador introduzir no sistema parâmetros como: o tempo e a potência de soldadura, bem como o tempo de arrefecimento;
- através do painel HMI instalado na máquina, o operador pode guardar muitos programas de soldadura para diferentes tipos de materiais, para não falar dos programas utilizados para trabalhar com diferentes tipos de eléctrodos;
- a máquina está equipada com o elétrodo de terra adicional, de modo a proteger o utilizador contra o aumento do nível de radiações não ionizantes HF emitidas pela máquina;
- ZTG HF AutoTuning System™ - a máquina está equipada com o sistema de controlo automático da potência de saída para aumentar a segurança do operador;
- ZTG SafeDOWN™ - a máquina está equipada com o sistema que deve proteger eficazmente o operador contra o elétrodo quando este está a ser baixado;
- ZTG Flash™ - outro sistema da máquina que se destina a proteger o elétrodo e a matéria-prima a soldar dos possíveis danos causados por um arco voltaico;
- Todas as máquinas receberam os Certificados de Conformidade CE
TECNOLOGIA DE ALTA FREQUÊNCIA:
A soldadura de alta frequência, conhecida como soldadura por radiofrequência (RF) ou soldadura dieléctrica, é o processo de fusão de materiais através da aplicação de energia de radiofrequência na área a unir. A soldadura resultante pode ser tão forte como os materiais originais.
A soldadura HF baseia-se em determinadas propriedades do material a soldar para provocar a geração de calor num campo elétrico rapidamente alternado. Isto significa que apenas determinados materiais podem ser soldados com esta técnica. O processo consiste em submeter as peças a unir a um campo eletromagnético de alta frequência (mais frequentemente 27,12 MHz), que é normalmente aplicado entre duas barras metálicas. Estas barras funcionam também como aplicadores de pressão durante o aquecimento e o arrefecimento. O campo elétrico dinâmico provoca a oscilação das moléculas dos termoplásticos polares. Dependendo da sua geometria e momento de dipolo, estas moléculas podem traduzir parte deste movimento oscilatório em energia térmica e causar o aquecimento do material. Uma medida desta interação é o fator de perda, que depende da temperatura e da frequência.
O policloreto de vinilo (PVC) e os poliuretanos são os termoplásticos mais comuns a serem soldados pelo processo RF. É possível soldar por RF outros polímeros, incluindo nylon, PET, PET-G, A-PET, EVA e algumas resinas ABS, mas são necessárias condições especiais, por exemplo, o nylon e o PET são soldáveis se forem utilizadas barras de soldadura pré-aquecidas para além da potência de RF.
A soldadura por alta frequência não é geralmente adequada para PTFE, policarbonato, poliestireno, polietileno ou polipropileno. No entanto, devido às restrições iminentes na utilização do PVC, foi desenvolvido um tipo especial de poliolefina que tem a capacidade de ser soldado por RF.
A função principal da soldadura HF é formar uma junta em duas ou mais espessuras de material em chapa. Existem várias características opcionais. A ferramenta de soldadura pode ser gravada ou perfilada para dar um aspeto decorativo a toda a área soldada ou pode incorporar uma técnica de gravação para colocar letras, logótipos ou efeitos decorativos nos elementos soldados. Ao incorporar uma aresta de corte adjacente à superfície de soldadura, o processo pode simultaneamente soldar e cortar um material. A aresta de corte comprime o plástico quente o suficiente para permitir que o material excedente seja arrancado, pelo que este processo é muitas vezes referido como soldadura de selagem.
ATENÇÃO: O fabricante não pode ser responsabilizado por quaisquer danos ou ferimentos resultantes de uma utilização incorrecta desta máquina.
ATENÇÃO: Para utilizar a máquina de uma forma óptima e segura, leia atentamente e siga todas as instruções incluídas neste Manual de Operação e Manutenção.
ATENÇÃO: Todos os operadores, com formação em segurança operacional, procedimentos operacionais e risco da máquina de soldar, bem como os qualificados para operar a máquina de soldar, são solicitados, pelo Contratante, a assinar, com a sua assinatura legível, o formulário em anexo.
ATENÇÃO: A máquina de soldadura de alta frequência foi concebida e produzida numa versão que não é adequada para pessoas com deficiência. Se a máquina for operada por pessoas com deficiência, a máquina deve ser devidamente adaptada após consulta do fabricante.
2.0 Sinais de segurança e pictogramas
2.1 Informações gerais
Para utilizar a máquina de soldar de forma óptima e segura, leia atentamente e siga todas as instruções incluídas neste Manual de Operação e Manutenção e, em particular, todas as informações e sinais de aviso, proibição, restrição e ordem.
Com base nas informações contidas neste Manual de Operação e Manutenção, o Cliente deve elaborar Manuais de Postos de Trabalho para os funcionários.
O Cliente é total, legal e materialmente responsável por todos e quaisquer eventos resultantes do conhecimento insuficiente deste Manual de Operação e Manutenção ou da não observância dos princípios da Segurança e Saúde no Trabalho.

ATENÇÃO: Antes de iniciar qualquer trabalho de qualquer pessoa que opere a máquina de soldar HF, é obrigatório familiarizar-se com o Manual de Operação e Manutenção.
ATENÇÃO: Qualquer destinatário ou pessoa autorizada pelo destinatário com base no presente Manual de Operação e Manutenção e nas características adequadas da tecnologia de produção é obrigatoriamente devido emitir o MANUAL DE TRABALHO para os operadores.
ATENÇÃO: A máquina de soldadura de alta frequência só pode ser operada por trabalhadores que tenham recebido formação sobre a manutenção do aparelho e sobre SEGURANÇA INDUSTRIAL, tendo especialmente em conta os possíveis riscos provenientes da máquina.
ATENÇÃO: Durante toda a vida útil da máquina, o Fabricante do aparelho sugere ao Comprador que utilize o pessoal de assistência técnica formado e fornecido pelo Fabricante ou as equipas de assistência técnica autorizadas pelo Fabricante.
ATENÇÃO: O fabricante recomenda vivamente que a máquina de soldar seja instalada apenas em ambiente industrial.
ATENÇÃO: A máquina deve estar corretamente nivelada e deve ter um local de funcionamento fixo.
ATENÇÃO: O manuseamento descuidado da máquina durante o transporte (deslocação) pode provocar ferimentos graves ou acidentes.
ATENÇÃO: O gerador é alimentado pela tensão perigosa para a vida da rede eléctrica 3 x220 VAC; 50 Hz. O aparelho tem uma alta tensão de até 5000 VDC. Todas as actividades de manutenção ou prevenção só podem ser executadas por pessoal formado e com a autoridade exigida por lei.
ATENÇÃO: O comprador deve ter o cuidado de executar corretamente e controlar regularmente a prevenção da instalação da proteção contra choques eléctricos para cada aparelho utilizado. Toda a responsabilidade nesta matéria é da responsabilidade do comprador.
ATENÇÃO: A tensão da lâmpada deve ser a mesma que a especificada na ficha de dados do produto - é possível ajustá-la utilizando ramos no lado primário do transformador incandescente.
ATENÇÃO: A lâmpada deve ser pré-aquecida durante cerca de uma hora após a instalação.
ATENÇÃO: Qualquer trabalho dentro da zona da unidade de prensagem ativa da prensa, ou seja, a substituição do dispositivo, só pode ser executado com medidas de precaução especiais por uma equipa de assistência treinada.
ATENÇÃO: A paragem de emergência da máquina é possível em qualquer momento, premindo a tecla EMERGENCY Botão STOP (o botão vermelho com fundo amarelo).
ATENÇÃO: O ambiente de trabalho da máquina, o chão e os suportes e pegas manuais devem estar sempre limpos e isentos de qualquer contaminação, gordura ou lama, de modo a reduzir ao mínimo possível o risco de escorregamento ou queda.
CUIDADO: Desligue a máquina da tomada antes de retirar quaisquer painéis de acesso ou abrir portas. Todas as protecções e painéis de acesso devem estar no lugar antes de utilizar esta máquina.
ATENÇÃO: A temperatura do elétrodo é de até 100 °C. Por conseguinte, quando tocado, pode queimar-se.
ATENÇÃO: A lâmpada contém metais de terras raras e óxidos de metais de terras raras que são altamente tóxicos. Em caso de quebra, a lâmpada deve ser eliminada com o máximo cuidado e com a ajuda de especializado serviços.
ATENÇÃO: A máquina de soldar de alta frequência é a fonte de radiação electromagnética não iónica. Após a instalação da máquina no local do comprador, deve ser efectuada a medição da radiação não-iónica. As medições de radiação devem ser efectuadas por uma empresa autorizada.
ATENÇÃO: As máquinas de soldar por alta frequência devem funcionar num local de trabalho firme, uma vez que a transposição exige novas medições da intensidade da radiação não-iónica.
ATENÇÃO: É proibido às pessoas com um pacemaker implantado permanecerem na zona de radiação ativa.
ATENÇÃO: O fabricante sugere que não sejam empregadas mulheres grávidas ou lactantes na zona de radiação não-iónica ativa.
ATENÇÃO: A máquina de soldadura de alta frequência foi concebida e produzida numa versão que não é adequada para pessoas com deficiência. Se a máquina for operada por pessoas com deficiência, a máquina deve ser devidamente adaptada após consulta do fabricante.


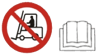

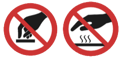



























3.0 Dados técnicos
Tipo de máquinatipo |
ZD-NX-4 |
Materiais de soldadura |
PVC, tecidos revestidos de PVC |
Alimentação eléctrica |
3 x 220 V; 50/60Hz |
Saída de potência HF |
4 kW |
Controlador PLC |
Delta |
Tensão de controlo |
24 VDC |
Capacidade instalada |
6 kVA |
Ajuste da capacidade de saída |
manual/autotuner |
Corte principal |
D25 A; diferido |
Frequência de funcionamento |
27,12 MHz |
Estabilidade da frequência |
+/- 0.6 % |
Sistema anti-flash, ZEMAT TG |
sensor ARC ultrarrápido e sensível |
Consumo de ar comprimido |
11 nl/ciclo |
Tamanho da mesa de trabalho |
800 x 410 mm |
Superfície de soldadura |
100mm^2 |
Curso do atuador |
~ 100mm |
Acionamento do elétrodo de pressão |
pneumático |
Acionamento do elétrodo de terra |
pneumático |
Força de pressão (máx.) |
1200 kG |
Lâmpada do gerador |
ITL 12-1 |
Líquido de refrigeração |
ar |
Peso da máquina |
~ 3500 kg |
Dimensões |
VER APÊNDICES |
4.0 Descrição técnica
O elemento principal da máquina de soldar de alta frequência ZD-NX-4 é a estrutura de suporte de carga feita de chapas e secções de aço soldadas. Todas as outras peças da máquina são montadas na referida estrutura. A estrutura de suporte de carga pode ser dividida em duas partes básicas:
- A parte traseira é onde se encontra o gerador de alta frequência juntamente com o transformador de ânodo e a caixa de interruptores. Esta parte está encerrada nas blindagens amovíveis protegidas pela chave do interrutor de fim de curso.
- a parte da frente, onde se encontra a mesa de trabalho sobre a qual é empilhado o material a soldar. A soldadura é feita quando o elétrodo é pressionado contra a mesa pela pinça isolada ligada à alavanca de pé pela placa intermédia. Acima da mesa, há um painel de controlo HMI
As protecções aplicadas juntamente com as teclas de comutação têm como objetivo minimizar a emissão de radiação não ionizante. É estritamente PROIBIDO operar a máquina de soldar sem as protecções!!!
- SISTEMA DE CONTROLO composto por PLC e painel tátil HMI, componentes de controlo e manipulação colocados no painel de controlo principal e outros equipamentos eléctricos e electrónicos colocados na máquina
- O AR COMPRIMIDO é composto, entre outros, por uma unidade de preparação de ar comprimido, válvulas de desvio e actuadores pneumáticos.
- O GERADOR é constituído por um gerador de alta frequência auto-excitado de constantes de desintegração que consiste principalmente no circuito LC de elevado fator Q fixado em 27,30MHz. O sistema consiste também no tubo de ondas progressivas, no transformador de ânodo, no transformador de filamento e no sistema de arrefecimento do tubo;
As protecções aplicadas juntamente com as teclas de comutação têm como objetivo minimizar a emissão de radiação não ionizante. É estritamente PROIBIDO operar a máquina de soldar sem as protecções!!!
A máquina utiliza plenamente os seguintes sistemas:
- A unidade de comando constituída pelo autómato com o painel tátil HMI, os comandos e os indicadores colocados no painel de comando principal ligado ao braço de extensão e os outros aparelhos eléctricos e electrónicos instalados nesta máquina; e
- A unidade de ar comprimido que consiste principalmente no conjunto de preparação do ar comprimido, incluindo: válvulas de distribuição e actuadores pneumáticos; e
- O GERADOR consiste num gerador auto-excitado de alta frequência de constantes de desintegração que consiste principalmente no circuito LC de elevado fator Q regulado para 27,30MHz. O sistema consiste também no tubo de ondas viajantes, no transformador de ânodo, no transformador de filamento e no sistema de arrefecimento do tubo;
O porta-eléctrodos de soldadura está equipado com um sistema de pega automática controlado a partir do painel tátil HMI. Permite a substituição dos eléctrodos sem ferramentas.
As protecções aplicadas juntamente com as teclas de comutação têm como objetivo minimizar a emissão de radiação não ionizante. É estritamente PROIBIDO operar a máquina de soldar sem as protecções!!!
Além disso, existem indicadores laser instalados no chassis da máquina para facilitar o posicionamento do material soldado na mesa de trabalho.
5.0 Montagem e instalação
5.1 Informação e sinalização das restrições e dos imperativos
O Fabricante fornece uma embalagem adequada da máquina para o momento do transporte. O tipo e a durabilidade da embalagem são adaptados à distância e ao meio de transporte e, consequentemente, ao risco potencial de danos durante o transporte. O Fabricante sugere que cada Cliente utilize os meios de transporte e o pessoal de assistência técnica do Fabricante.
O armazenamento da máquina não implica quaisquer requisitos especiais, para além de um ambiente de armazenamento adequado.
O local de armazenamento deve garantir uma proteção suficiente contra os factores climáticos, deve ser o mais seco possível e ter um nível de humidade aceitável (inferior a 70%). É igualmente necessário assegurar uma proteção adequada contra a corrosão, especialmente no que diz respeito aos componentes metálicos que não são pintados por razões técnicas.
Se a máquina for fornecida numa caixa e for envolvida em plástico que gera uma atmosfera anticorrosiva, a máquina deve permanecer envolvida e embalada durante todo o período de armazenamento.
Para efeitos de proteção contra a humidade, recomenda-se que a máquina não seja armazenada diretamente no chão do armazém, mas sim sobre paletes.
Um componente que requer atenção e manuseamento especiais em todas as fases - incluindo a armazenagem - é a lâmpada do gerador (tríodo). A lâmpada deve ser armazenada na sua embalagem original, na posição vertical, com o ânodo virado para cima ou para baixo, numa sala seca. A lâmpada é um componente metálico e cerâmico de alto vácuo, extremamente frágil e que não pode ser atingido ou deixado cair mesmo de uma altura baixa.
Bater, deixar cair, abanar ou inclinar a lâmpada durante um período de tempo mais longo pode provocar, e normalmente provoca, danos permanentes e irreversíveis na lâmpada. Em particular, o filamento do cátodo da lâmpada pode ser quebrado, o que, em casos mais extremos, pode levar a curto-circuitos internos ou à quebra da lâmpada.
ATENÇÃO: A lâmpada contém metais de terras raras e óxidos de metais de terras raras que são altamente tóxicos. Em caso de quebra, a lâmpada deve ser eliminada com o máximo cuidado e com a ajuda de serviços especializados.
As disposições acima referidas destinam-se a instruir e a advertir todas as pessoas e serviços que possam ter contacto com esta unidade relativamente à sua elevada vulnerabilidade a todos os impulsos e pancadas. Ao mesmo tempo, não serão aceites quaisquer reclamações relacionadas com os danos permanentes acima descritos no decurso do processo de reclamação.
É também de salientar que a lâmpada do gerador é um componente muito dispendioso.
Em caso de dúvida, recomenda-se que consulte o pessoal especializado do Fabricante.
5.2 Transporte da máquina
A parte responsável pelo transporte e pela instalação da máquina nas instalações do Adquirente deve ser determinada na fase de assinatura do contrato e, o mais tardar, após o teste de aceitação final da máquina nas instalações do Fabricante, antes de o dispositivo ser entregue ao Adquirente.
ATENÇÃO: O manuseamento descuidado do aparelho durante o transporte/deslocação pode provocar ferimentos graves ou acidentes.
É PROIBIDO montar, desmontar ou transportar a máquina por pessoal sem qualificações adequadas ou sem estar familiarizado com os requisitos de segurança descritos no presente Manual de Operação e Manutenção. Estas acções podem provocar acidentes ou danos materiais.
Tendo em conta o carácter específico do dispositivo, o Fabricante sugere que cada Adquirente utilize os meios de transporte e o pessoal do serviço técnico do Fabricante.
O tubo de alimentação deve ser desmontado antes de qualquer ação de transporte ou movimentação.
A lâmpada deve ser sempre transportada ou deslocada na embalagem original do fabricante, na posição vertical, com o ânodo virado para cima ou para baixo, sem bater ou sacudir a lâmpada.
ATENÇÃO: A máquina deve ser transportada na posição vertical.
Devido ao seu tamanho e estrutura, a máquina requer a desmontagem e a desconexão de alguns componentes e unidades durante o transporte ou a deslocação. É necessário desmontar os componentes e ferramentas frágeis e dispendiosos (que devem ser transportados numa mala separada). É absolutamente necessário desmontar a lâmpada do gerador.
A máquina deve ser deslocada utilizando dispositivos de elevação - gruas, empilhadores, porta-paletes - com capacidade de elevação suficiente para permitir o transporte seguro do gerador, enquanto as pessoas que operam esses dispositivos de elevação devem possuir todas as licenças e qualificações válidas exigidas por lei.
Todos os componentes da máquina susceptíveis de serem danificados durante o transporte (se não for utilizada uma caixa de embalagem de elevada durabilidade) ou por dispositivos de elevação ou de deslocação devem ser adequadamente fixados (desde que sejam desmontados e embalados separadamente).
Para garantir uma posição estável do dispositivo, é muito importante assegurar uma proteção adequada da máquina durante o transporte longo (cintos de segurança, parafusos de ancoragem), bem como proteção e assistência durante o transporte no local.
Se a máquina não estiver equipada com acessórios apropriados, é possível utilizar quaisquer outros orifícios disponíveis ou elementos de durabilidade suficiente para garantir que o gerador e outras partes da máquina estão corretamente equilibrados e estabilizados.
O peso da máquina (cerca de 350 kg) deve ser definitivamente tido em conta ao planear o transporte.
5.3 Instalação no local de funcionamento
Em função do grau de complexidade da máquina, a instalação no local de utilização deve ser efectuada pelo pessoal do Adquirente, depois de ter lido este Manual de Utilização e Manutenção, ou pelo pessoal do serviço técnico do Fabricante, em colaboração com o pessoal do Adquirente.
Lembre-se de que o posicionamento e a instalação adequados da máquina de soldar são vitais para garantir o seu funcionamento ótimo, bem como o conforto e a segurança do operador no ambiente do dispositivo.
O Adquirente é responsável pela preparação do local para a instalação do dispositivo, pela disponibilidade e preparação das ligações eléctricas e pela realização dos requisitos específicos do projeto técnico e dos testes de aceitação técnica que aprovam todo o gerador para utilização.
O fabricante fornecerá ao autor da encomenda todas as instruções e informações necessárias a este respeito.
ATENÇÃO: Certifique-se de que o chão/superfície/fundações em que a máquina vai ser colocada têm durabilidade suficiente, tendo em conta o peso, a superfície e a distribuição do peso da máquina pelos seus pontos de apoio (normalmente as pernas).
ATENÇÃO: O aparelho deve estar corretamente nivelado e deve ter um local de funcionamento fixo.
O local ideal de funcionamento da máquina de soldar HF é a superfície de betão não coberta ou coberta com uma camada muito fina de material não condutor.
A superfície deve ser feita de acordo com o projeto específico, seguindo as normas de construção e segurança, bem como os requisitos relativos às posições paralelas, perpendiculares e planas.
ATENÇÃO: O Adquirente é o único responsável pelo cumprimento das condições acima mencionadas.
Após a colocação da máquina de soldar no local selecionado, é necessário nivelar a máquina, verificar o seu estado técnico e remover todos e quaisquer defeitos que possam ter ocorrido durante o transporte. De seguida, desembalar, posicionar, nivelar e fixar o gerador. A lâmpada do gerador de alta frequência deve ser montada no final do processo de instalação. Esta tarefa deve ser feita com especial atenção, quer na montagem da lâmpada no casquilho/base, quer na ligação dos contactos eléctricos da lâmpada. Ligar os conectores da consola de comando às tomadas devidamente marcadas na prensa. Recomenda-se que a instalação da máquina após o transporte seja efectuada sob a supervisão direta de um representante do fabricante.
ATENÇÃO: Se as tarefas acima mencionadas forem executadas por um representante do Cliente, devem ser realizadas estritamente de acordo com a descrição contida neste Manual de Operação e Manutenção e/ou instruções fornecidas pelo fabricante durante o teste de aceitação técnica.
A máquina de soldar só pode ser utilizada em locais sem poeiras, ácidos, enxofre, fumos cáusticos e gases inflamáveis. Devido ao campo magnético gerado, os objectos metálicos de grandes dimensões não devem ser colocados perto da máquina de soldar. A máquina pode afetar o funcionamento de dispositivos electrónicos (rádio, televisores, computadores) localizados perto da máquina, devido à elevada sensibilidade de entrada dos referidos dispositivos. O local ideal de funcionamento da máquina é a superfície de betão não coberta ou coberta com uma camada muito fina de material não condutor.
5.4 Instalação no local de funcionamento
5.4.1 Instalação no local de funcionamento
ATENÇÃO: O fabricante recomenda vivamente que a máquina seja instalada apenas em ambiente industrial.
A máquina objeto do presente manual de instruções e de manutenção foi concebida e fabricada para trabalhar em ambiente industrial para o processamento de correias transportadoras.
As condições específicas de funcionamento dos dispositivos, ou seja, humidade do ar elevada, temperatura elevada, vapor e poeiras, foram tidas em conta pelos projectistas da máquina e não afectam o seu funcionamento, mas determinam requisitos mais rigorosos relativamente à execução de programas preventivos.
A máquina não pode ser utilizada em atmosferas potencialmente explosivas, atmosferas muito poeirentas, ambientes com elevada humidade e/ou temperatura elevada e presença de fumos agressivos (ácidos, básicos, orgânicos ou inorgânicos, com impacto potencial ou factualmente corrosivo).
A temperatura do ambiente de trabalho deve variar entre +10º C e +40º C e a humidade relativa entre 30% e 90%. Não é permitida a condensação de humidade atmosférica ou de quaisquer substâncias agressivas sobre a superfície da máquina (ou de qualquer um dos seus componentes).
É necessário que a amplitude térmica a longo prazo durante o dia na sala de operação do gerador não exceda 10º C e no caso da humidade relativa: 10%.
A cláusula anterior não se aplica aos meios ou substâncias utilizados para lubrificação, conservação ou substâncias não agressivas utilizadas no decurso da produção/funcionamento do dispositivo.
ATENÇÃO: Se houver uma grande diferença entre a temperatura exterior e a temperatura da divisão onde a máquina está instalada, o aparelho deve ser colocado em funcionamento 24 horas após a sua montagem na divisão.
5.4.2 Iluminação
Os requisitos relativos à intensidade luminosa mínima estabelecem que, na área de funcionamento horizontal, a iluminação que pode ser aceite em salas onde as pessoas permanecem durante um período de tempo mais longo, independentemente da realização de quaisquer actividades visuais, deve ser de 300 lx.
No caso de actividades visuais cujo nível de dificuldade seja superior à média e quando seja necessária uma visão muito confortável, bem como quando a maioria dos operadores tenha mais de 40 anos, a intensidade luminosa exigida deve ser superior à mínima, ou seja, pelo menos 500 lx.
5.4.3 Ruído
A máquina não produz ruídos de nível que exijam a utilização de quaisquer meios ou dispositivos de proteção do pessoal.
No entanto, é necessário ter em conta que todos os ambientes de trabalho têm as suas próprias emissões sonoras, que podem ter um impacto no nível de ruído emitido pela máquina durante o seu funcionamento.
5.5 Parâmetros de ligação
5.5.1 Energia eléctrica
Ligação: 3 x 2200V; 50Hz (3P+N+PE), proteção contra sobreintensidades com propriedades retardadas. A instalação do Cliente deve garantir medidas de proteção contra choques eléctricos em conformidade com a norma EN 60204-1:2018-12.
ATENÇÃO: Verificar sempre a tensão do filamento após a instalação do tubo - ver dados técnicos do tubo.
5.5.2 Ar comprimido
Pressão: 0,4 - 0,8 MPa, classe de limpeza exigida de acordo com a norma ISO8573-1 4-4-4, consumo: 11 nl por um ciclo.
ATENÇÃO: Se a pressão no sistema do utilizador final for superior a 0,8 MPa, deve ser reduzida para cerca de 0,8 MPa com uma válvula redutora montada na ligação da máquina de soldar.
5.6 Parâmetros de ligação
Dependendo da complexidade do sistema e das qualificações e licenças dos empregados, a ligação da máquina de soldar no local de funcionamento é efectuada por pessoas seleccionadas pelo Adquirente ou por trabalhadores do serviço técnico do Fabricante, em cooperação com o pessoal do Adquirente, por um preço adicional ou gratuitamente, o que é sempre combinado antes de a máquina ser entregue ao Adquirente a partir das instalações do Fabricante.
É sempre necessário verificar se todas as ligações foram efectuadas de acordo com a documentação do aparelho.
É de referir que as tarefas acima mencionadas exigem qualificações adequadas do pessoal, incluindo as licenças aplicáveis emitidas pelos organismos competentes.
Aplica-se tanto a qualificações especializadas, como a cursos de formação concluídos e válidos em matéria de saúde e segurança no trabalho, incluindo, em particular, os riscos envolvidos nessas tarefas.
6.0 Funcionamento
6.1 Preparação da máquina para o funcionamento - Primeira colocação em funcionamento
Procedimento de Controlo Pré-Operação:
- controlar e verificar a eficácia das medidas de proteção contra os choques eléctricos
- controlar e verificar a tensão de alimentação - valor e correção da ligação das fases, se for caso disso sentido de rotação do motor
- verificar a tensão da lâmpada de incandescência
- retirar as protecções da máquina de soldar e verificar se não existem pequenos danos (os fios não estão partidos, as ligações roscadas não estão soltas, etc.)
- desembalar, verificar e instalar as lâmpadas do gerador.
ATENÇÃO: Para utilizar a máquina de uma forma óptima e segura, leia atentamente e siga todas as instruções incluídas neste Manual de Operação e Manutenção.
É PROIBIDO executar qualquer trabalho na máquina de soldadura por pessoas que não tenham recebido formação prévia no serviço de máquinas de alta frequência e nas normas de Segurança Industrial, com especial atenção aos possíveis riscos provenientes da máquina.
Desde que todos os requisitos de instalação tenham sido cumpridos e as tarefas descritas no ponto 5 tenham sido executadas, estamos prontos para iniciar a máquina de soldar pela primeira vez no ambiente de produção do local do Adquirente.
ATENÇÃO: O primeiro arranque da máquina deve ser efectuado na presença e sob a supervisão dos representantes do Fabricante.
6.2 Requisitos de funcionamento - Instruções e directrizes gerais
Todas as regulações e calibrações necessárias ao correto funcionamento dos parâmetros do dispositivo foram efectuadas pelo Fabricante durante os procedimentos de montagem e de testes internos. A conformidade geral com os requisitos técnicos contratuais e o correto funcionamento da máquina são confirmados durante a aceitação técnica que tem lugar nas instalações do Fabricante, na presença de um representante do Adquirente, e utilizando matérias-primas originais entregues pelo Adquirente para efeitos de ensaio.
ATENÇÃO: Devido às propriedades específicas dos dispositivos que emitem energia de alta frequência, é necessário efetuar determinadas medições no local de funcionamento do dispositivo no sítio do Adquirente. Pela mesma razão, é muito importante que a máquina tenha um local de funcionamento fixo.
Antes do início da utilização da máquina e da sua primeira colocação em funcionamento, o Destinatário é absolutamente obrigado a formar os trabalhadores que serão os seus futuros operadores.
ATENÇÃO: A máquina de soldar SÓ pode ser operada por trabalhadores que tenham recebido formação em manutenção da máquina e SEGURANÇA INDUSTRIAL, com especial atenção aos possíveis riscos provenientes da máquina. Esta formação deve ser confirmada através de um documento adequado assinado por uma pessoa com formação.
Além disso, devido aos diferentes ciclos de trabalho efectuados pelas nossas máquinas em vários ambientes industriais, o Destinatário tem a obrigação absoluta de criar um MANUAL DE OPERAÇÃO claro e transparente para o dispositivo, adaptado aos seus próprios ciclos de produção.
ATENÇÃO: O comprador ou a pessoa autorizada pelo comprador é obrigado a emitir um MANUAL DE SUPORTE DE TRABALHO com base neste Manual de Operação e Manutenção e nas características da tecnologia de produção.
Devido às propriedades específicas dos aparelhos que emitem energia de alta frequência, é necessário efetuar determinadas medições no local de funcionamento do aparelho nas instalações do Adquirente. Pela mesma razão, é muito importante que a máquina tenha um local de funcionamento fixo.
ATENÇÃO: A máquina de soldar de alta frequência é a fonte de radiação electromagnética não iónica. Após a instalação do aparelho no local do comprador, deve ser efectuada a medição da radiação não-iónica. As medições de radiação devem ser efectuadas por uma empresa autorizada e definir os limites da área perigosa.
ATENÇÃO: A máquina deve ter um local de trabalho permanente. Cada mudança de localização do aparelho exige medições especializadas adequadas e a determinação das zonas de impacto do campo eletromagnético não ionizante.
ANTES DA OPERAÇÃO É ABSOLUTAMENTE NECESSÁRIO CONTROLAR:
- Eficácia das medidas de proteção contra choques eléctricos;
- Tensão da fonte de alimentação - valor e correção da ligação das fases;
- Direção de rotação do motor (se aplicável);
- Tensão da lâmpada de filamento incandescente;
ATENÇÃO: A tensão da lâmpada deve ser a mesma que a especificada na ficha de dados do produto - é possível ajustá-la utilizando ramos no lado primário do transformador incandescente.
ATENÇÃO: Devido ao carácter específico do dispositivo, é sempre necessário avisar e informar o pessoal sobre a elevada tensão de alimentação do ânodo da lâmpada e o risco potencial de choque elétrico fatal por corrente eléctrica de tensão até 5000 VDC.
ATENÇÃO: A lâmpada deve ser pré-aquecida durante cerca de uma hora após a instalação.
- Posição do suporte na base da mesa de trabalho;
- Emissão de campo eletromagnético - após o ajuste dos parâmetros de soldadura, durante o processo de soldadura;
INSTALAÇÃO DA LÂMPADA DO GERADOR
- retirar o escudo de proteção lateral do gerador, constituído por uma chapa metálica perfurada
- retirar o tubo de plástico que dirige o fluxo de ar
- colocar a lâmpada no casquilho - a lâmpada só pode ser colocada no casquilho de uma forma (não aplicar força excessiva)
- montar o tubo de plástico que dirige o fluxo de ar
- colocar e fixar o fecho do sensor de temperatura no ânodo
- certificar-se de que o interrutor de fim de curso do sensor do cabo está ligado
- fixar as folhas de alimentação do condensador de distribuição e do condensador de disco à parte superior do ânodo
- não alterar a forma ou a posição dos componentes metálicos no interior dessa câmara do gerador
- ligar o sistema de alimentação eléctrica à rede de alimentação eléctrica, assegurando a qualidade adequada do sistema de proteção contra choques eléctricos
- ligar o circuito incandescente e a unidade de controlo, colocando o INTERRUPTOR PRINCIPAL na posição I-ON. A lâmpada de controlo SUPPLY deve acender-se (se for necessário, premir o botão azul RESET na cassete de controlo);
ATENÇÃO: A ventoinha de arrefecimento da lâmpada é ligada quando se liga o circuito luminoso da lâmpada do gerador. Se a unidade de ventilação não funcionar, não utilizar a máquina até que a avaria da unidade de ventilação seja eliminada!!!
- verificar a tensão de incandescência da lâmpada do gerador. Esta deve manter-se dentro do intervalo exigido pelo fabricante do tríodo. Se necessário, pode ser ajustada mudando os ramos do transformador. Estas tarefas devem ser executadas por um representante do Fabricante da máquina ou (por conta e risco do Cliente) por outra pessoa com as qualificações adequadas, ou seja, com um certificado emitido pela Associação de Electricistas apropriada (na Polónia SEP) e com conhecimentos sobre os perigos e riscos envolvidos na operação de uma máquina de soldadura de alta frequência, particularmente o risco potencial de eletrocussão pela tensão de até 5000 V. Uma lâmpada nova deve ser acesa durante cerca de 0,5 h antes de o circuito do ânodo ser ligado
- testar o funcionamento da unidade de controlo de acordo com o procedimento descrito no ponto 6
- após o ajustamento dos parâmetros de soldadura, durante o processo de soldadura, verificar a emissão do campo eletromagnético.
IMPORTANTE: Se os circuitos de alta tensão tiverem sido acidentalmente ligados quando o ânodo estiver desligado ou se a lâmpada do gerador estiver defeituosa, os condensadores do filtro de alta tensão devem ser descarregados através de um curto-circuito com o invólucro durante um período muito curto.
ATENÇÃO: Todas as actividades durante o arranque e as medições, quando o nível de segurança é mais baixo (ecrãs de proteção abertos, interruptores de chave bloqueados), devem demorar o mínimo de tempo possível, e o nível de segurança de funcionamento completo da máquina deve ser assegurado o mais rapidamente possível.
ATENÇÃO: Todas as actividades de controlo e medição devem ser realizadas depois de se verificar se os interruptores para a regulação da tensão anódica estão na posição 0 - OFF (não se aplica à medição da emissão do campo eletromagnético).
ATENÇÃO: Todas as actividades de controlo e medição devem ser realizadas exclusivamente por pessoal autorizado.
É SEMPRE PROIBIDO iniciar o processo de soldadura, ou seja, ligar a alta tensão da lâmpada, que inicia a tensão de alta frequência no suporte isolado do elétrodo, quando o nível de segurança do funcionamento do aparelho é reduzido.
A máquina está adaptada para trabalhar no ciclo automático. O modo automático é o modo normal de funcionamento do aparelho durante o processo de produção.
A máquina de soldadura de alta frequência permite o funcionamento em modo manual para efeitos de regulação.
Os operadores de máquinas devem usar sempre vestuário de trabalho normal e calçado antiderrapante.
O ambiente de trabalho do dispositivo, o chão e os suportes e pegas manuais devem estar sempre limpos e isentos de qualquer contaminação, gordura ou lama, de modo a reduzir ao mínimo possível o risco de escorregamento ou queda.
Nunca utilizar a máquina de trabalho sem os elementos de proteção fixos ou móveis. Verificar regularmente se todos os ecrãs de proteção e todos os outros elementos de proteção estão bem montados e funcionam corretamente.
Apenas pessoas autorizadas, com formação adequada sobre o funcionamento da máquina e sobre Segurança e Saúde no Trabalho, podem ter contacto direto com a máquina.
Cada operador do aparelho deve ser instruído sobre as funções dos elementos de proteção da máquina e a sua utilização correcta.
Na área circundante do aparelho (cerca de 1,5 m à volta do gerador e da prensa), não pode haver objectos que possam interferir com o funcionamento do aparelho. Esta zona deve ser mantida limpa e ter uma iluminação adequada.
Nunca utilizar os manipuladores da máquina ou os tubos flexíveis como suportes. Lembre-se de que qualquer movimento acidental do manipulador do aparelho pode iniciar acidentalmente o processo de soldadura, alterar os parâmetros ou mesmo provocar a avaria da máquina ou danificar as suas ferramentas.
É OBRIGATÓRIO informar o supervisor e/ou o pessoal de trânsito sobre todo e qualquer caso de funcionamento incorreto do aparelho.
É ESTRITAMENTE PROIBIDO retirar as coberturas de proteção durante o funcionamento da máquina.
É ESTRITAMENTE OBRIGATÓRIO utilizar TODAS as capas de proteção e botões de bloqueio concebidos
Nunca utilizar a máquina de trabalho sem os elementos de proteção fixos ou móveis. Verificar regularmente se todos os ecrãs de proteção e todos os outros elementos de proteção estão bem montados e funcionam corretamente.
Na área circundante do aparelho (cerca de 1,5 m à volta do gerador e da prensa), não pode haver objectos que possam interferir com o funcionamento do aparelho. Esta zona deve ser mantida limpa e ter uma iluminação adequada.
O ambiente de trabalho do dispositivo, o chão e os suportes e pegas manuais devem estar sempre limpos e isentos de qualquer contaminação, gordura ou lama, de modo a reduzir ao mínimo possível o risco de escorregamento ou queda.
6.3 Controlos e indicadores disponíveis para o operador
Todos os comandos e indicadores da máquina de soldar podem ser facilmente encontrados na sua construção ou na sua mesa de controlo. Antes de começar a trabalhar, o operador da máquina deve familiarizar-se com a disposição dos comandos e indicadores na máquina, bem como com as funções que estes controlam.
A lista completa dos controlos e indicadores acima mencionados, disponíveis para o operador, encontra-se em anexo:
- INTERRUPTOR PRINCIPAL - o interrutor que está instalado na parte da frente da caixa da máquina, é utilizado para ligar e desligar a alimentação eléctrica. A posição 1- ON significa que o interrutor está ligado, enquanto a posição 0-OFF significa que o interrutor está desligado.
- NÍVEL DE POTÊNCIA - o comutador está instalado na parte da frente da caixa da máquina o controlo da tensão escalonada é utilizado para a regulação da tensão do ânodo Ua. Comuta os ramos do transformador de ânodo (O interrutor passa de 0 a 1, 2 onde: 0 - significa que o transformador do ânodo está desligado, 1 - significa que o nível de tensão do ânodo é o mais baixo, 2 - significa que o nível de tensão do ânodo é o mais alto).
- PAINEL DE CONTROLO HMI - o painel PLC, constituído por um ecrã de cristais líquidos no qual se encontram os parâmetros de soldadura programados e os botões de pressão que podem ser utilizados caso os parâmetros devam ser visualizados.
- PARAGEM DE EMERGÊNCIA - o botão de paragem de emergência vermelho com cabeça de cogumelo que deve ser utilizado para parar a máquina em caso de avaria ou acidente.
- USB - Porta USB para transferência de receitas e histórico de alarmes. Situada no painel de controlo ou no lado direito da máquina. O serviço de arquivo de dados é descrito no capítulo 6.5. A porta é um equipamento adicional da máquina.
- CORRENTE AN ÓDICA - o amperímetro de painel, que pode ser encontrado no painel de controlo (Fig. 8), deve medir a corrente eléctrica num circuito anódico e deve permitir a avaliação visual do processo de soldadura (características de carga do gerador).
- REGULAÇÃO DA PRESSÃO - a válvula redutora de pressão de comando manual (Fig. 8) é uma válvula utilizada para a regulação da pressão no sistema pneumático da máquina (puxar a válvula para cima e rodar: uma volta para a direita - maior pressão, uma volta para a esquerda - menor pressão), a pressão nominal de funcionamento da máquina é de 6 bar;
O nível de pressão no sistema pneumático nunca excede o nível de pressão que impulsiona a máquina.
- INDICADOR DA POSIÇÃO DO INTERRUPTOR DE LIMITE INFERIOR - um recorte na placa com uma escala, que permite observar a posição do indicador vermelho e, portanto, observar a posição da altura do interrutor de limite inferior, facilitando assim a sua regulação na posição inferior.
- RESET - o botão de pressão azul, que se encontra no posto de comando (Fig. 10), deve ser utilizado no caso de a máquina ter de ser reiniciada devido a um acidente de avaria ou de ser ligada. A implementação do procedimento de reteste de todos os sistemas de alarme é fortemente aconselhada a ser posta em prática sempre que a máquina for ligada.
- STOP - o botão preto (Fig. 10), que se encontra na estação de controlo, deve ser utilizado para parar o processo de soldadura de alta frequência.
- INICIAR - Para obter a soldadura de alta frequência, devem ser utilizados dois botões de pressão verdes, que se encontram na estação de controlo (Fig. 10) (os dois botões devem ser premidos simultaneamente).
- COLUNA DE SINALIZAÇÃO LUMINOSA
- A. A cor vermelha indica uma falha e, ao mesmo tempo, a mensagem de alarme deve ser apresentada no painel sensível ao toque da HMI.
As mensagens de alarme são apagadas e a luz vermelha na coluna de sinalização luminosa deixa de piscar quando o botão RESET é premido. No caso de os esforços terem sido em vão e a mensagem de alarme não ter sido apagada quando o botão RESET foi premido, isso pode significar que a causa da ocorrência da avaria ainda não foi eliminada.
- A cor laranja indica que a máquina de soldar de alta frequência começa a funcionar
- A cor verde indica que a máquina está pronta para trabalhar.
- A. A cor vermelha indica uma falha e, ao mesmo tempo, a mensagem de alarme deve ser apresentada no painel sensível ao toque da HMI.
- SISTEMA DE PREPARAÇÃO DO AR COMPRIMIDO (Fig. 12) - é constituído por
- o terminal de ar comprimido ao qual deve ser ligada a mangueira de ar comprimido. A mangueira deve fornecer ao sistema o ar comprimido de 4 a 8 bar
- a válvula de corte do ar comprimido accionada manualmente (para abrir a válvula - rodá-la para a esquerda e colocá-la na posição ON; uma volta para a direita - a posição OFF - a válvula está fechada)
- a válvula redutora de pressão de comando manual é uma válvula utilizada para regular a pressão no sistema pneumático da máquina (puxar a válvula para cima e rodar: uma volta para a direita - maior pressão, uma volta para a esquerda - menor pressão), a pressão nominal de funcionamento da máquina é de 6 bar
O nível de pressão no sistema pneumático nunca excede o nível de pressão que impulsiona a máquina.
- o filtro de ar comprimido juntamente com o mecanismo de libertação da água de condensação
- o manómetro que indica o nível de pressão no sistema de ar comprimido da máquina
- Limitador de pressão do elétrodo - aparafusado na haste do pistão do atuador, foi concebido para limitar o curso do comprimento do atuador e é suposto evitar que o material de soldadura seja "espremido" por baixo do elétrodo.
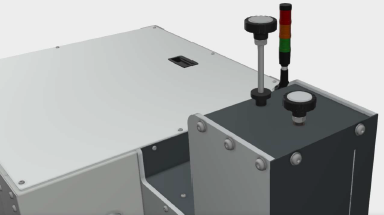
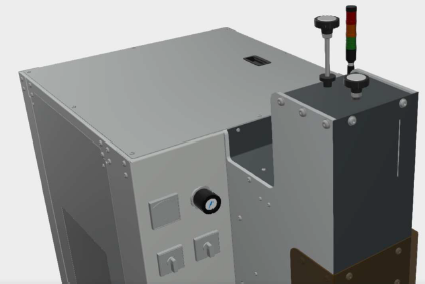
- posicionar o material na mesa de trabalho - como na soldadura
- utilizando a alavanca de pé, baixar o suporte com o elétrodo sobre o material (de modo a que o elétrodo apenas toque no material sem exercer qualquer força de pressão) e deixá-lo
- rodando o botão, mova o interrutor de fim de curso de forma a que o seu rolo fique sobre o indicador de altura do elétrodo. Apertar o botão
- levantar o suporte do elétrodo para a sua posição superior utilizando a alavanca de pé
- baixar o suporte do elétrodo com a alavanca de pé, pressionar o suporte do elétrodo contra o material e verificar se o rolo do interrutor pára no suporte do elétrodo

O procedimento de regulação adequada do sistema de controlo da altura:
- posicionar o material na mesa de trabalho - como na soldadura
- utilizando a alavanca de pé, baixar o suporte com o elétrodo sobre o material (de modo a que o elétrodo apenas toque no material sem exercer qualquer força de pressão) e deixá-lo
- rodando o manípulo (manípulo marcado com uma seta na Fig. 14), deslocar o interrutor de fim de curso de modo a que o seu rolo fique sobre o indicador de altura do elétrodo. Apertar o botão
- levantar o suporte do elétrodo para a sua posição superior utilizando a alavanca de pé
- baixar o suporte do elétrodo com a alavanca de pé, pressionar o suporte do elétrodo contra o material e verificar se o rolo do interrutor pára no indicador de altura do elétrodo e se o alerta é apresentado no painel HMI na janela principal .

6.5 Programação e utilização da consola tátil HMI
ATENÇÃO! Cada valor do parâmetro representado nos gráficos deste manual é tomado ao acaso e deve ser ignorado pelo operador da máquina. Os valores dos parâmetros devem derivar da experiência prática do utilizador, uma vez que podem variar profundamente em função do tipo de material soldado ou da instrumentação implementada.
No painel HMI, todos os valores editáveis dos parâmetros são apresentados num fundo branco. Para visualizar um parâmetro, o utilizador tem de premir o seu valor e, como resultado, o teclado no ecrã deve ser aberto. Os dados podem ser guardados premindo a tecla Enter.
6.5.1 Ligação à fonte de alimentação
Pouco depois de a máquina ser ligada a uma fonte de alimentação, aparece no ecrã HMI uma janela de alarme com a seguinte mensagem:
#K001 BOTÃO DE REPOSIÇÃO DE PRESSÃO
De acordo com esta situação, a máquina precisa de ser reiniciada, pelo que a tecla azul RESET deve ser premida. De seguida, é necessário aguardar 30 segundos até que a máquina esteja pronta para trabalhar e entre em modo stand-by, o que se verificará pela seguinte sequência de eventos: um indicador luminoso na coluna de sinalização luminosa pisca a verde e a barra de progresso azul, na margem superior da janela do painel HMI, desaparece. Caso a massagem de alarme não desapareça do ecrã do HMI, ver capítulo 6.5.2.
Para verificar se o sinal de alarme é apresentado, o
botão na parte superiordo menu deve ser premida; se não houver mensagens, os gráficos mudarão para
6.5.2 Mensagens de alarme
Quando ocorre uma avaria na máquina ou quando um dos sistemas de proteção é ativado ou quando são detectadas outras anomalias no funcionamento da máquina, é apresentada uma das mensagens de alarme no painel sensível ao toque da HMI. Todas as mensagens de alarme são apagadas com a ajuda da tecla RESTART .

Os tipos de massagens de alarme:
#Esta mensagem indica que a causa de pelo menos uma das mensagens de alarme, atualmente apresentadas, deixou de existir. Premir o botão azul de RESET para colocar a máquina no estado de pronta.
#A001 PARAGEM DE EMERGÊNCIA - é apresentado quando:
- a máquina está ligada - o circuito de segurança da máquina deve ser sempre verificado quando a tecla RESET é premida
- o botão vermelho de PARAGEM DE EMERGÊNCIA, com cabeça de cogumelo, foi premido e ficou encravado. É necessário desbloqueá-lo, rodando a cabeça para a direita.
#A002 TEMPERATURA DO TUBO - este tipo de massagem significa que o arrefecimento do tubo da onda viajante não existe ou que o sistema de arrefecimento falhou e é apresentado quando o sistema de proteção térmica do tubo é colocado em funcionamento, o que significa que o tubo da onda viajante aqueceu a uma temperatura demasiado elevada e, como resultado, o contrapino da banda do tubo que tinha sido ligado ao interrutor de limite por um cabo ficou dessoldado.
Um contrapino é soldado a uma banda do tubo com a ajuda de uma solda de ponto de fusão muito inferior àquele em que o tubo foi sobreaquecido (danificado). Se a temperatura da lâmpada subir demasiado, o contrapino cairá da banda e, em consequência, o interrutor de fim de curso será acionado, sendo simultaneamente apresentada a mensagem de alarme e cortada a alimentação de energia para um brilho no tubo. Em seguida, a causa do sobreaquecimento deve ser eliminada.
ATENÇÃO! O cabo não deve ser fixado a nenhuma outra parte da máquina, exceto ao contrapino da fita que foi aparafusada ao tubo. A inobservância do aviso citado pode resultar num bloqueio do interrutor de limite, o que pode levar ao sobreaquecimento do tubo da onda viajante e, em consequência disso, à sua danificação.
If the cotter pin gets separated from the band, the band should be taken off from the tube, the pin should be soldered to the band with the standard solder used in electronic engineering (Melting point <190oC) so that the repaired part could be reattached to the tube.
O sobreaquecimento do tubo pode ser causado por:
- a sujidade encontrada no gerador ou no radiador do tubo
- a avaria da ventoinha de arrefecimento do tubo ou a avaria do sistema de alimentação da ventoinha
- o entupimento dos orifícios de ventilação da máquina ou o excesso de terra recolhida pelos filtros instalados nos orifícios de ventilação
- a temperatura ambiente excessiva.
#A003 ANTIFLASH - este tipo de mensagem significa que o sistema de proteção contra um arco voltaico durante a soldadura foi ativado - devido a esta mensagem, certifique-se de que nem a almofada de isolamento, nem o material soldado, nem o elétrodo de soldadura foram danificados.
#A004 SOBRECARGA DO ÂNDO - esta mensagem significa que o limite de subida do ânodo foi excedido, pelo que os parâmetros aplicáveis à energia libertada na soldadura têm de ser ajustados.
#A006 PRESSÃO DE AR BAIXA - esta mensagem significa que há falta de pressão de ar ou que o nível de pressão de ar é demasiado baixo no sistema pneumático. Certifique-se de que a mangueira que fornece o ar comprimido está ligada à máquina ou que o nível de ar comprimido é adequado e, em seguida, com a ajuda do regulador da válvula redutora de pressão, que pode ser encontrado no sistema de preparação do ar comprimido, ajuste a pressão na máquina para o nível adequado.

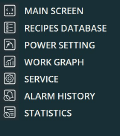





6.5.4 Ecrã principal
Receita - sob este nome pode ser encontrado um grupo de parâmetros que se aplicam ao ciclo de trabalho. Uma vez estabelecidos os parâmetros de soldadura para o tipo específico de produto, resultantes da experiência prática (os valores dos parâmetros dependem fortemente do tamanho da soldadura, do tamanho do material soldado e da forma do elétrodo), devem ser introduzidos no sistema e guardados com o nome da receita.
Adicionalmente, dois valores ao lado do nome de cada parâmetro também podem ser encontrados no ecrã HMI. O primeiro (sobre o fundo azul) é o valor do parâmetro de funcionamento atual apresentado em tempo real, o segundo (sobre o fundo branco) é o valor definido a partir da receita de produção ou dos dados do operador.
Se for necessário, o operador pode sempre premir o dígito no fundo branco e alterar o seu valor. O valor do parâmetro de funcionamento atual é imediatamente atualizado, embora a alteração não afecte a receita executada.
Para guardar as alterações efectuadas numa receita através do ecrã principal, prima o botão GUARDAR RECEITA
para copiar os parâmetros do ecrã principal para a barra Editar fórmula na janela Base de dados de fórmulas. Os parâmetros copiados podem ser guardados como uma nova receita utilizando o botão Criar nova receita ou podem ser utilizados para atualizar uma receita existente utilizando o botão Atualizar.
Nome: - o nome da receita executada para efeitos de produção.
Potência inicial - este parâmetro indica a posição (capacidade) do condensador de saída que se encontra no gerador; a intensidade da corrente anódica na fase inicial da soldadura de alta frequência depende fortemente do valor deste parâmetro. (Parâmetro expresso em valores percentuais, em que 0% indica o nível mais baixo de capacidade - o nível mais baixo de intensidade de corrente anódica e 100% indica o nível mais alto de capacidade - o nível mais alto de intensidade de corrente anódica).
-
O valor do parâmetro Potência inicial e o valor da corrente anódica (potência libertada no material) não são linearmente dependentes, pelo que devem ser tomadas as medidas de precaução adequadas ao ajustar os valores deste parâmetro.
O valor atual do parâmetro Potência inicial e o valor do parâmetro de ajuste são iguais um ao outro apenas na fase inicial do procedimento de soldadura. Quando o procedimento é iniciado, a posição do condensador de saída é automaticamente ajustada de modo a atingir a potência de funcionamento.
Potência de funcionamento - este parâmetro indica a corrente do ânodo I utilizada para a soldadura. (Parâmetro expresso em valores de amperes que variam de 0 a 4 A).
Os valores a verde na escala do medidor de corrente anódica indicam os valores aceitáveis da corrente anódica Ia.
Quando o procedimento de soldadura é iniciado, o condensador de saída (potência inicial) é automaticamente ajustado de modo a atingir a potência de funcionamento.
Tempo de atraso - este parâmetro indica o tempo durante o qual o elétrodo aderiu ao material soldado antes do início da soldadura. (Parâmetro expresso em segundos, com valores que variam de 0 a 99 s).
Tempo de soldadura - este parâmetro significa o tempo que a máquina demora a processar a soldadura de alta frequência. (Parâmetro expresso em segundos, com valores que variam de 0 a 99 s).
Tempo de arrefecimento - este parâmetro indica o tempo durante o qual o elétrodo foi pressionado contra o material soldado depois de a soldadura ter terminado - o material arrefece ao ser pressionado contra a mesa. (Parâmetro expresso em segundos com valores que variam de 0 a 99 s.).
Modo corrente: 1 - O modo de soldadura do tipo corrente significa que o contador da máquina começa a contar o tempo de soldadura de alta frequência que foi introduzido no parâmetro Tempo de soldadura assim que a máquina obtém o valor apropriado da corrente do ânodo La que deve ser superior ou igual ao valor introduzido no parâmetro Potência de funcionamento. Por outras palavras, no modo de soldadura de tipo corrente, o tempo de soldadura é igual à soma do valor do tempo que a máquina leva para produzir a corrente anódica (o valor introduzido no parâmetro Potência de funcionamento) e o valor do tempo introduzido no parâmetro Tempo de soldadura.
Se a máquina não conseguir atingir a potência de funcionamento no prazo de 25 segundos, inicia a contagem decrescente do tempo de aquecimento, depois completa o ciclo e, por fim, apresenta uma mensagem sobre o facto de não ter atingido a potência de funcionamento.
0 - O modo de soldadura do tipo tempo significa que o tempo de soldadura de alta frequência é igual ao valor introduzido no parâmetro da receita com o nome Tempo de soldadura.
Vale a pena notar que, no modo de soldadura do tipo tempo, o ciclo de trabalho pode ser executado mesmo que a máquina não consiga produzir a potência de funcionamento, pelo que a soldadura obtida pode ter uma resistência irregular.
Regulação do condensador:
1 - significa que, durante a soldadura, o condensador de saída é ajustado automaticamente para que a corrente do ânodo esteja ao nível definido no parâmetro Potência de funcionamento.0 - indica que a máquina está a trabalhar no modo de regulação automática limitada do condensador de saída. Durante a soldadura, o condensador de saída é ajustado apenas quando a corrente do ânodo excede o valor inserido no parâmetro Power max.
Ao trabalhar na Regulação do Condensador - 0, note que se a Potência inicial for demasiado baixa, a máquina não será capaz de ajustar automaticamente a corrente do ânodo Ia para cima para atingir o valor definido no parâmetro Corrente do ânodo.
Correção de potência - este parâmetro refere-se ao método de controlo do condensador de saída na fase inicial, quando, após a ligação do ciclo de soldadura, o condensador visa obter a Corrente de Funcionamento. O parâmetro permite que a regulação do condensador seja desactivada sem atingir a corrente de funcionamento definida.
- Exemplo 1: A corrente de trabalho definida é 1A, a posição de arranque é 40%, a regulação do condensador é 1, a correção de potência é 0A.
- Depois de ligar o ciclo de soldadura, a corrente de funcionamento é de 0,5 A.
- Inicia-se o ajuste do condensador de saída, de modo a atingir o objetivo de 1A de corrente de funcionamento.
- A posição do condensador muda de 40% para 75% - A corrente de funcionamento atinge o valor 1 A; as regulações do condensador param.
- O ciclo de soldadura continua.
- Exemplo 2: A corrente de funcionamento está definida para 1 A; a posição de arranque está definida para 40%; a regulação do condensador está definida para 1; a correção de potência está definida para -0,2 A.
- Depois de o ciclo de soldadura ter sido ligado, a corrente de funcionamento atinge o nível de 0,5 A.
- Inicia-se o ajuste do condensador de saída, de modo a atingir uma corrente de funcionamento alvo igual a 1A, menos o valor de correção de potência, que é 1A - 0,2A = 0,8A.
- A posição do condensador muda de 40% para 60% - A corrente de funcionamento passa a ser de 0,8 A; a regulação do condensador pára.
O parâmetro de correção de Potência é utilizado em processos de soldadura em que, na fase inicial, a Corrente de Trabalho é baixa, seguida de um aumento muito dinâmico da corrente. A sobreposição do aumento espontâneo da Corrente de Trabalho e da regulação do condensador, provocando o seu aumento, conduz a um valor inaceitavelmente elevado de Corrente de Trabalho. Se a regulação do condensador de saída for desligada antes de se atingir o valor regulado da corrente de funcionamento, a corrente pode atingir espontaneamente o valor requerido.
A maioria dos processos de soldadura não requerem a utilização da correção de potência; o parâmetro deve então ser definido para 0.
Os parâmetros da receita - nível de potência e pressão - com o comentário apresentado a amarelo (SET MANUALLY) são apenas uma informação para o operador que, ao ler os parâmetros no ecrã tátil, deve alterar manualmente as definições na parte lateral da máquina. A alteração desta definição no ecrã não afecta as definições da máquina!
Nível de potência - é a principal definição da potência da máquina; o ajuste é efectuado alterando a tensão do ânodo Ua no intervalo de 1 a 2, em que 1 é potência baixa e 2 é potência máxima: 0 - o transformador do ânodo está desligado.
ATENÇÃO! É importante lembrar que, apesar de os parâmetros acima mencionados poderem ser guardados sob o nome da receita no painel tátil da HMI, existem ainda dois outros parâmetros, tais como PRESSÃO e TEMPERATURA DO ELETRODO que devem ser ajustados manualmente.
O valor da tensão do ânodo Ua deve ser selecionado experimentalmente em função da superfície da soldadura e do tipo de material de soldadura.
PRESSÃO - - o parâmetro indica a pressão do ar comprimido no sistema pneumático de fixação do elétrodo, expressa em bares na gama de 0 - 6 bar; o parâmetro determina a força de descida do elétrodo em relação ao material durante a soldadura.
O nível de pressão no sistema pneumático com a ajuda do qual o elétrodo é pressionado contra a mesa nunca excede o nível de pressão que impulsiona a máquina
Depois de definir o nível de potência e a pressão no painel HMI no ecrã principal, será apresentada uma janela (Fig. 17) que informa o operador de que o valor destes parâmetros deve ser ajustado manualmente (utilizando um interrutor adequado) e que deve ser confirmado com o botão de confirmação.
Alerta de elétrodo em posição descendente será apresentado quando o elétrodo atingir a posição inferior (movimento no sensor)
Ciclos efectuados: - significa o contador dos ciclos de soldadura executados na máquina. Se o operador mantiver premido o botão Botão de reposição do contador
durante 3 segundos, o contador é reposto a zero.
MENSAGENS DE ALARME QUE INFORMAM SOBRE A AUSÊNCIA DE CONDIÇÕES PARA INICIAR O CICLO DE SOLDADURA:
NOT READY - indica que a máquina não foi reiniciada corretamente e não teve um arranque que durou alguns segundos. Prima o botão RESET no painel de controlo. O estado do arranque, que é o tempo de aquecimento da lâmpada, é apresentado como uma barra de progresso na parte superior do ecrã.
6.5.5 Base de dados de receitas
Base de dados de receitas.
Todas as receitas guardadas na memória da consola HMI são apresentadas sob a forma de uma coluna LISTA DE RECEITAS. Os parâmetros das receitas são descritos no capítulo anterior. O número de receitas é praticamente ilimitado. O conteúdo da receita é apresentado à direita; clicando nos valores sobre o fundo branco, é possível alterar os valores dos parâmetros.
NOVA RECEITA: Para criar uma nova receita, preencher todos os campos dos parâmetros da receita e, em seguida, premir o botão
. Aparecerá uma nova receita na lista de receitas.
Para guardar as alterações efectuadas numa receita com o Ecrã principal, prima o botão GUARDAR RECEITA botão
para copiar os parâmetros do ecrã principal para o ecrã Editar receita bar no Base de dados de receitas janela. Os parâmetros copiados podem ser guardados como uma nova receita com a tecla Criar novo ou podem ser utilizadas para atualizar uma receita existente utilizando o botão Atualização botão.
Se a lista de receitas já contiver uma receita com o mesmo nome que a receita a guardar, não será possível guardar a nova receita, mas apenas atualizar os parâmetros. Neste caso, alterar o nome da receita.
EDIÇÃO DE RECEITAS
Para editar uma receita, é necessário clicar no nome da receita a partir da lista de receitas (a receita selecionada deve ser destacada a amarelo e apresentada em Editar receita linha). No que respeita a uma alteração do valor do parâmetro em Editar receita Para editar uma linha, é necessário clicar na caixa branca onde esta deve ser apresentada e introduzir um novo valor. Uma vez concluído o procedimento de edição, o ecrã Atualização a tecla deve ser premida
e, consequentemente, as alterações introduzidas na receita indicada serão aceites, guardadas e armazenadas.
Para guardar os parâmetros da receita a partir do ecrã principal, prima o botão GUARDAR RECEITA
visível nesta janela. Se existir uma receita com o mesmo nome na lista de receitas, os seus parâmetros serão actualizados.
PROCEDIMENTO DE SUPRESSÃO
Para efetuar o procedimento de eliminação de uma receita, clicar no nome da receita que consta da lista de receitas (a receita selecionada deve ser destacada a amarelo e apresentada na linha Editar receita ) e, em seguida, premir a tecla Delete.
PROCEDIMENTO DE SELECÇÃO DE RECEITAS
Para realizar o procedimento de seleção de receitas para fins de produção, selecionar na lista de receitas a receita com os valores necessários para o ciclo de trabalho (a receita selecionada deve ser destacada a amarelo e apresentada em Editar receita linha) e clique em Carga para produção
como resultado, a receita será carregada no sistema e preparada para ser utilizada na produção atual, sendo os seus parâmetros apresentados no Ecrã principal janela.
PROCESSO DE TRIAGEM
As receitas utilizadas para a produção estão listadas por ordem alfabética. Se houver mais receitas, aparece uma barra de deslocação ao lado da tabela, que permite percorrer a tabela sem problemas. Também é possível ordenar as receitas por nome, de forma ascendente ou descendente. Para ordenar as receitas, clique no cabeçalho da lista - Lista de receitas; uma segunda pressão mudará a direção da ordenação. Todos os dados são guardados na memória da consola HMI. Na pasta "Receita" existem dois ficheiros de receitas: "Receita.db" e "Receita_a.rcp". É possível editar receitas no computador. É possível copiar ficheiros de receitas da memória do painel tátil para uma pen USB e editá-los, utilizando o programa gratuito EasyBuider Pro. Estes ficheiros podem ser utilizados como cópia de segurança das receitas ou para carregar receitas para outro painel tátil HMI.
6.5.6 Definição de potência
Definição de potência.
Existem dois indicadores na janela:
Corrente an ódica - um indicador da intensidade da corrente anódica. Indica a intensidade da corrente anódica La, que deve ser igual à intensidade da corrente do medidor analógico que se encontra no painel de controlo.
CAPACITOR - uma ferramenta que indica a posição do condensador de saída (no intervalo de 0 a 100%). Com a ajuda desta ferramenta, é possível definir o nível adequado de potência - regra geral, quanto maior for a capacidade, maior será a corrente anódica La.
Um grupo de teclas sob o indicador é utilizado para o ajuste do condensador do ânodo. O ajuste pode ser efectuado de duas formas:
AUTO - antes da soldadura, o condensador é automaticamente colocado na posição correspondente aos valores introduzidos no Potência inicial parâmetro. Quando o procedimento de soldadura é executado, a posição do condensador é automaticamente ajustada de modo a que o nível de intensidade da corrente do ânodo La possa subir para o valor inscrito no parâmetro Potência de funcionamento parâmetro.
Escolha o modo de definição AUTO durante os ciclos de trabalho normais efectuados pela máquina. O modo MANUAL é utilizado para procedimentos de teste.
MANUAL - todo o processo de regulação do condensador é efectuado à mão; quando necessário, o operador pode alterar a posição do condensador com a ajuda de
ou
e, ao mesmo tempo, a intensidade da corrente anódica é ajustada.
Potência máx. = Potência de funcionamento + ... - o parâmetro define o valor máximo pelo qual a POTÊNCIA DE FUNCIONAMENTO pode ser excedida para iniciar a diminuição automática da corrente anódica com a utilização do condensador de saída (parâmetro definido em amperes, na gama de 0 - 1A). Potência min. = Potência de funcionamento - ... - o parâmetro define o valor mínimo pelo qual a POTÊNCIA DE FUNCIONAMENTO pode ser excedida para iniciar o aumento automático da corrente anódica com a utilização do condensador de saída (parâmetro definido em amperes, no intervalo de 0 - 1A).
6.5.7 Gráfico de trabalho
Gráfico de trabalho.
A janela contém um gráfico que mostra em pormenor o funcionamento da máquina. É possível observar a evolução de dois parâmetros em tempo real:
- as alterações na corrente do ânodo (linha vermelha);
- as alterações na posição do condensador de saída (linha azul).
O gráfico mostra dados registados no passado. No canto superior direito existe um botão que abre uma janela na qual é possível selecionar o período a partir do qual os dados devem ser apresentados e as definições de visualização do gráfico podem ser alteradas.
6.5.8 Menu Serviço
- Exemplo 1: A corrente de trabalho definida é 1A, a posição de arranque é 40%, a regulação do condensador é 1, a correção de potência é 0A.
-
Menu de serviço.
Nesta janela são apresentadas as seguintes informações de origem estatística:
Contagem de ciclos - é o número total de ciclos de funcionamento desde que a máquina foi ligada pela primeira vez.
Tempo de trabalho - é o tempo total de trabalho da máquina,
Antiflash - este valor indica quantas vezes, desde o dia em que a máquina foi fabricada, o sistema de proteção contra arco voltaico foi ligado.
Alarme de sobrecarga do ânodo - este valor indica quantas vezes, desde o dia em que a máquina foi fabricada, foi excedido o nível máximo de intensidade de corrente no circuito do ânodo e, consequentemente, quantas vezes foi ativado o mecanismo de proteção contra a sobrecarga do ânodo.
Alarme de sobrecar ga da rede - este valor indica quantas vezes, desde o dia em que a máquina foi fabricada, foi excedido o nível máximo de intensidade de corrente no circuito da rede durante a soldadura e, consequentemente, quantas vezes foi ativado o mecanismo de proteção contra a sobrecarga da rede.
Alarme de temperatura do tubo - este valor indica quantas vezes, desde o dia em que a máquina foi fabricada, o sistema de proteção térmica do tubo foi automaticamente acionado.
Os parâmetros listados abaixo estão disponíveis apenas para os técnicos de serviço do fabricante, razão pela qual é necessária uma palavra-passe para editar os parâmetros.
Controlo do processo ativo - ativa
ou desativar
as configurações de controlo do ciclo HF para a corrente de trabalho (ânodo), durante o processo de soldadura. Por outras palavras, a seleção do botão resulta no facto de que, durante o processo de soldadura, o intervalo de tolerância +/- da corrente do ânodo, especificado na janela de serviço nos parâmetros de controlo do processo de soldadura, foi observado. Os parâmetros de controlo são descritos mais adiante neste manual.
-
Potência máx = Potência de funcionamento + - este parâmetro indica o valor máximo de intensidade de corrente que pode exceder o valor do limite de potência de funcionamento para iniciar o procedimento automático de descida da corrente anódica efectuado pelo condensador de saída (parâmetro expresso em amperes no intervalo de 0 a 1A).
Potência min = Potência de funcionamento - . .. - Este parâmetro só é utilizado para controlar o processo de soldadura e para determinar a gama inferior de tolerância de corrente
-
Tempo de atraso da pressão - este valor indica a quantidade de tempo que decorre desde o momento em que o interrutor de limite inferior (que indica a posição inferior do elétrodo) é acionado até ao momento em que o elétrodo é pressionado contra o material com força total.
Definir % de soldadura na tolerância: - este parâmetro especifica o valor percentual do tempo durante o qual a corrente deve estar dentro da tolerância. Quando o limiar de percentagem prescrito não é atingido, é apresentado um alarme no painel HMI, indicando que os parâmetros de soldadura não foram atingidos: #A013 PARÂMETROS DE SOLDADURA NÃO ATINGIDOS. Nas estatísticas, a coluna Estado do ciclo indica 0 para o ciclo atualmente em curso.
Tempo total de soldadura [s]: - este parâmetro mostra o tempo total gasto pela última soldadura.
Tempo de soldadura na tolerância [s]: - Este parâmetro mostra o tempo da última soldadura; no entanto, só é contado para a corrente dentro do intervalo de tolerância +/- (Potência máx/min) prescrito nos parâmetros acima.
-
Percentagem de soldadura na tolerância [%] - Este parâmetro mostra a percentagem de tempo durante o qual a corrente esteve dentro do intervalo de tolerância +/- durante todo o ciclo que foi recentemente efectuado na máquina. Em caso de alarme, é possível diagnosticar rapidamente que percentagem do tempo de soldadura foi atingida para os parâmetros acima mencionados.
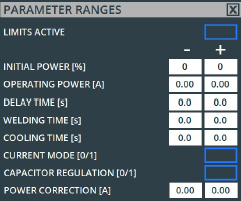



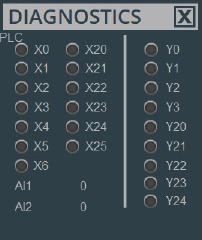


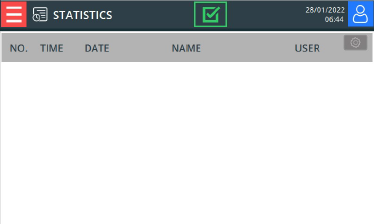
Time - hora a que o registo foi efectuado
Potência de funcionamento [A] - valor do parâmetro utilizado no processo
Regulação do condensador [0/1] - valor do parâmetro utilizado no processo
- o parâmetro Modo de corrente foi definido para 0 - a média é contada a partir do momento em que a alta frequência foi ligada
- o parâmetro Modo de corrente está definido para 1 - a média é contada a partir do momento em que o valor definido da corrente de funcionamento foi obtido;
Contador de ciclos - valor indicado no contador de ciclos desde o primeiro arranque da máquina
OPERADOR A INICIAR SESSÃO
O painel tátil pode ser protegido contra o acesso não autorizado. Para ativar ou desativar a função de início de sessão do utilizador, vá à janela de serviço e clique na área marcada a vermelho abaixo:
Abre-se a seguinte janela:
Início de sessão ativo - botão ativa ou
desactiva o processo de registo. Para alternar entre funcionalidades, deve ser introduzida a palavra-passe 21369.
A seguir são apresentadas as mensagens que aparecem na máquina, consoante o utilizador esteja a iniciar sessão, a adicionar um novo utilizador, a eliminar um utilizador, a alterar as permissões do utilizador ou a alterar uma palavra-passe.
- Sucesso! (pode aparecer ao iniciar sessão, adicionar novos utilizadores, eliminar utilizadores, alterar as permissões do utilizador, alterar a palavra-passe).
- Palavra-passe incorrecta! (só pode aparecer ao iniciar a sessão).
- A conta já existe! (só pode aparecer quando se adiciona um utilizador).
- Caracteres inaceitáveis na palavra-passe! (pode aparecer quando se adiciona um utilizador e se altera a palavra-passe).
- Caracteres inaceitáveis no nome! (só pode aparecer quando se adiciona um utilizador)
1. depois de ligar a máquina, clicar no botão "Log-in" na janela do painel tátil
2. Abre-se uma janela contextual para iniciar a sessão.
3. Seleccione um utilizador adequado na lista pendente.
4. Introduza a palavra-passe adequada e confirme-a com o botão Enter do teclado.
5. Prima o botão Iniciar sessão.
6. Aparecerá no ecrã uma mensagem adequada.
Depois de a máquina ser desligada, o utilizador é automaticamente desconectado.
CRIAR NOVOS UTILIZADORES
1. Inicie sessão como um utilizador com autoridade de gestão de utilizadores.
2. Selecionar o ícone
3. Introduzir o nome de um utilizador no campo do utilizador (letras e números)
4. Introduza a palavra-passe no campo da palavra-passe (letras e números)
5. Seleccione o nível de direitos que o utilizador a ser criado deve ter.
A - trabalhos de base na máquina
B - não atribuído
C - edição de receitas
D - não atribuído
E - não atribuído
F - parâmetros de serviço, gestão de utilizadores
6. Seleccione o botão Adicionar.
7. Aparecerá no ecrã uma mensagem adequada.
APAGAR UTILIZADORES
1. Inicie sessão como um utilizador com autoridade de gestão de utilizadores.
2. Selecionar o ícone
3. Seleccione um utilizador adequado na lista pendente.
4. Prima o botão apagar.
5. Aparecerá no ecrã uma mensagem adequada.
ALTERAR AS PERMISSÕES ATRIBUÍDAS AO UTILIZADOR.
1. Inicie sessão como um utilizador com autoridade de gestão de utilizadores.
2. Selecionar o ícone
3. Seleccione um utilizador adequado na lista pendente
4. Selecionar ou anular a seleção do nível de autorização para um determinado utilizador.
5. Prima Alterar.
6. Aparecerá no ecrã uma mensagem adequada.
ALTERAR A PALAVRA-PASSE
1. Iniciar sessão. O operador só pode alterar a sua própria palavra-passe; no entanto, um supervisor pode alterar a palavra-passe de qualquer utilizador
2. Selecionar o ícone
3. Seleccione um utilizador adequado na lista pendente (se tiver iniciado sessão como supervisor).
4. Introduzir a Nova palavra-passe
5. Prima Alterar.
6. Aparecerá no ecrã uma mensagem adequada.
UTILIZADORES CRIADOS NA FÁBRICA E RESPECTIVA(S) PALAVRA(S)-PASSE ATRIBUÍDA(S)
NOME DO UTILIZADOR - PALAVRA-PASSE
OPERADOR - 33
SUPERVISOR - 11
Miller Weldmaster - DESTINADO AO SERVIÇO DO FABRICANTE;
Permissões:
OPERADOR - trabalho na máquina, capacidade de selecionar e editar receitas.
SUPERVISOR - trabalhar na máquina, selecionar uma receita, editar receitas, alterar parâmetros, adicionar e retirar operadores e alterar as palavras-passe de outros utilizadores.
Dados arquivados na memória do painel tátil da HMI

O seguinte software é necessário para ler e converter ficheiros de histórico e receitas num computador com sistema operativo Windows:
- o software gratuito EasyBuider Pro, que pode ser descarregado do painel HMI a partir da página web do fabricante: http://www.weintek.com/ ou do representante na Polónia http://www.multiprojekt.pl/ftp/weintek_hmi/easy_builder_pro/
- Microsoft Excel ou outro programa de folha de cálculo.
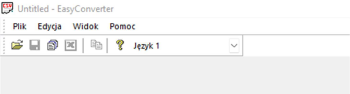
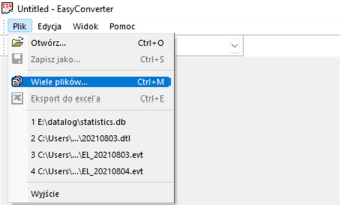
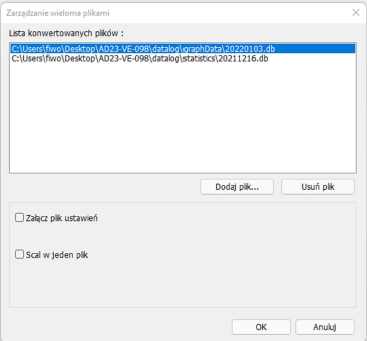
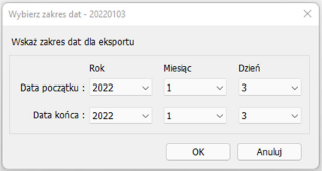
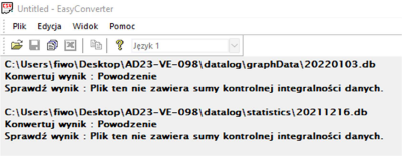
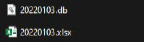
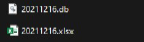
- No computador equipado com uma placa de rede sem fios, selecionar a rede com um nome correspondente ao número de fábrica da máquina, tal como consta da placa de identificação, por exemplo: D120-XM-003.
- Introduzir a palavra-passe correspondente ao número de fábrica da máquina em letras maiúsculas a partir do fim sem hífenes, por exemplo: 300MX021D.
- Aceda à janela de serviço e clique na área marcada a vermelho abaixo.
- Abre-se a janela com as configurações avançadas, na qual se encontra o endereço IP do painel HMI e o projeto atualmente carregado.
COPIAR FICHEIROS DO HISTÓRICO A PARTIR DO PAINEL HMI UTILIZANDO A REDE WI-FI
- Abrir o Explorador do Windows em qualquer pasta e introduzir a seguinte fórmula na barra de endereços onde se encontra o endereço IP, por exemplo: 192.168.1.50; deve ser introduzido o endereço lido no painel tátil: ftp://uploadhis:753456@192.168.1.50/
- Em seguida, clique em "Introduzir
- Abre-se uma janela que contém a memória do painel tátil
- A estrutura da pasta foi descrita num dos capítulos seguintes. O conteúdo completo de cada pasta pode ser copiado. Também é possível copiar ficheiros individuais que estão armazenados nas pastas.
DADOS ARQUIVADOS NA MEMÓRIA DO PAINEL TÁCTIL HMI
- Insira um dispositivo de memória USB na porta do painel tátil da HMI.
- Aparecerá uma janela no ecrã do painel HMI quando o botão Upload deve ser premido antes do fim da contagem decrescente.
- Na janela seguinte, seleccione os dados a descarregar e introduza a palavra-passe:
- 753456, seleccione a localização /usbdisk/disk_a_1 e prima o botão Upload para iniciar a transferência dos ficheiros.
A ESTRUTURA DOS FICHEIROS DE HISTÓRICO E DE RECEITAS
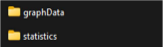
- "receita"- na pasta "receita" existem três ficheiros: "receita.db" "receita_a.rcp" e "receita.rcp". O ficheiro "recipe.db" contém as receitas guardadas na consola HMI. Pode ser utilizado como cópia de segurança ou para transferir receitas para outro painel tátil HMI. Também pode editar receitas no seu computador.
- "datalog" - na pasta "datalog" existe a pasta "graphData" e a pasta "statistics".
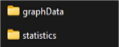
- "graphData" - na pasta "GraphData" encontram-se os ficheiros que contêm os registos dos parâmetros de funcionamento da máquina. Para cada dia de funcionamento da máquina, é guardado um ficheiro com o nome da data. Além disso, é registado o seguinte:
- C [%] - posição do condensador
- Ia [A] - intensidade da corrente anódica
Todos estes parâmetros são armazenados uma vez em cada 0,5 segundos e apenas durante o ciclo. São registados numa tabela.
- "estatísticas" - na pasta "estatísticas" existem ficheiros com registos de estatísticas do processo. Em cada dia de funcionamento da máquina, é guardado um ficheiro com o nome da data. Também é registado o seguinte:
- nome da receita - nome da receita utilizada para executar o ciclo de trabalho registado.
- utilizador - nome do operador com sessão iniciada durante o ciclo.
- capa position [%] - posição inicial pré-definida do condensador.
- corrente [A] - corrente de funcionamento definida.
- tempo de atraso [s] - tempo de atraso definido.
- tempo de soldadura [s] - tempo de aquecimento definido.
- cool time [s] - tempo de arrefecimento definido.
- nível de potência - nível de potência definido.
- pressão [bar] - pressão definida.
- modo atual - ponto de regulação do modo atual .
- regulação do condensador - ponto de regulação da regulação do condensador.
- correção atual - valor do parâmetro utilizado no processo.
- controlo do processo - informações sobre o controlo ativo do processo.
- estado do processo - estado do controlo do processo, em que -1 significa controlo inativo do processo,
- significa erro - processo interrompido ou parâmetros de soldadura não atingidos, 1 significa sucesso - o processo de soldadura decorreu, de acordo com os parâmetros definidos para a corrente.
- estado atual - estado do controlo atual, em que -1 significa controlo de processo inativo,
- significa erro - processo interrompido ou parâmetros de soldadura não atingidos, 1 significa sucesso - o processo de soldadura decorreu, de acordo com os parâmetros definidos.
- corrente média - valor médio da corrente durante a soldadura.
- contador - contador de ciclos da máquina.
- eventlog"- na pasta "eventlog" encontram-se os ficheiros com o registo do histórico das mensagens de alarme que foram visualizadas durante o funcionamento da máquina. O histórico das mensagens de alarme é guardado num ficheiro denominado EL_data, por exemplo: EL_20220105. Além disso, é registado o seguinte:
- Evento - informação, em que 0 indica quando a mensagem de alarme ocorreu e 2 indica quando a mensagem de alarme foi reposta
- Categoria - irrelevante
- Mensagem - o conteúdo da mensagem de alarme
- Ligue a memória USB com as receitas rasgadas ao computador e abra o programa Utility Manager.
- No canto superior esquerdo da janela, clique em Selecionar ecrã e seleccione o modelo do painel: cmt X Serie - Basic.
- No separador Conversão de dados, seleccione a aplicação Editor da base de dados de receitas.
- Na aplicação Editor da base de dados de receitas, clique em Importar... e seleccione os ficheiros com as receitas copiadas "receita.db".
- Abre-se a janela de edição da receita.
- Quando a edição estiver concluída, clique em Exportar... e guarde o ficheiro na sua localização anterior.
COPIAR RECEITAS DA MEMÓRIA USB:
- 1. Insira a pen USB com as receitas guardadas na tomada do painel tátil da HMI. O ficheiro da receita deve estar na pasta "receita" exatamente como está quando as receitas são descarregadas do painel
- No ecrã do painel HMI, aparece uma janela, clique em Descarregar.
- Na janela seguinte, seleccione Base de dados de receitas; seleccione a localização do ficheiro de receitas; introduza a palavra-passe: 753456 e clique no botão Transferir.
As receitas serão carregadas na memória do painel tátil da HMI. Desligar e voltar a ligar a máquina.
6.6 Ligação à fonte de alimentação
A máquina não deve, EM CIRCUNSTÂNCIA ALGUMA, ser operada por pessoal não qualificado. Os operadores da máquina devem estar familiarizados com as regras de segurança e saúde no trabalho.
Antes de ligar a máquina a uma fonte de alimentação, é necessário efetuar os seguintes procedimentos:
- certificar-se de que o ambiente de trabalho da máquina (a máquina e as suas imediações) está limpo e em ordem ou que não existem obstáculos que possam influenciar negativamente o ciclo de funcionamento normal da máquina; e
- certificar-se de que é preparada a quantidade adequada de matéria-prima (provetes); e
- certificar-se de que os caixotes do lixo e os contentores para produtos soldados estão colocados no local adequado, mas na proximidade da máquina, devido aos requisitos da Bayer aplicáveis ao ciclo de produção, caso existam; e
- O elétrodo de soldadura deve ser instalado numa pinça (a exceção à regra é quando o elétrodo é colocado no material e depois pressionado por uma pinça)
- certificar-se de que todas as protecções estão corretamente fixadas à máquina e que as portas laterais de uma caixa de distribuição estão fechadas;






- Levantar o elétrodo para a sua posição superior.
- Colocar o INTERRUPTOR PRINCIPAL na posição 0-OFF - significa que a máquina está desligada.
- Desligar a válvula manual de corte do ar comprimido (para efetuar o procedimento - rodar a válvula para a direita - posição OFF)
- Ordenar o ambiente de trabalho em torno da máquina.
- A ficha de alimentação eléctrica, bem como a ficha do sistema de ar comprimido, devem ser desligadas em caso de paragem prolongada do trabalho (ambas as fichas devem ser retiradas das tomadas).
O AJUSTAMENTO DO PARALELISMO DA MESA
No caso de haver correção do paralelismo entre a superfície de soldadura do elétrodo e a superfície da mesa de trabalho, recomenda-se o ajuste da posição do elétrodo utilizando parafusos de ajuste
A REGULAÇÃO DA ALAVANCA DO PÉ
O movimento para a frente ou para trás da alavanca de pé pode ser ajustado por meio de porcas, uma das quais está marcada com a letra A na Fig. 32. A outra porca encontra-se do lado oposto. A alavanca de pé tem também furos de ambos os lados para baixar a alavanca de pé, se necessário.
6.7 Procedimento de teste e regulação


O procedimento de ensaio e regulação deve ser posto em prática quando:
- a máquina foi ligada pela primeira vez,
- a substituição das ferramentas é necessária (quando necessário),
- o procedimento de manutenção está concluído,
- os operadores devem estar familiarizados com a funcionalidade da máquina.
Para efetuar o referido procedimento, o operador deve
1. Verificar se o interrutor Ua SETTING, que se encontra no lado da máquina, está na posição 0 - OFF.2. Dispor o material a soldar sobre a mesa de trabalho

3. Pressionar a alavanca de pé e o grampo com o elétrodo sobre o material.

7. Levantar e descer várias vezes a pinça com o elétrodo para verificar se este se move com fluidez, para verificar se o elétrodo está paralelo à mesa.





- POTÊNCIA INICIAL
- POTÊNCIA DE FUNCIONAMENTO
- TEMPO DE ATRASO
- TEMPO DE SOLDADURA
- TEMPO DE ARREFECIMENTO.
Quando um novo tipo de material é submetido a testes, recomenda-se vivamente que os parâmetros dos ciclos de soldadura de valores baixos sejam introduzidos no sistema e que os seus valores sejam gradualmente aumentados até se obter o efeito mais desejável da soldadura.
14. Ajustar o nível de pressão do elétrodo utilizado para o processo de soldadura com a ajuda da válvula redutora de pressão operada manualmente (Fig. 8 - dígito 7)
15. Premir no painel HMI: HMI → Ecrã principal → Modo atual → 0 ou 1
16. Premir no painel HMI: HMI → Ecrã principal → Regulação de condensadores →
O modo de corrente 0/1 e a regulação do condensador 0 / 1 são descritos em pormenor no capítulo 6.5.4.
17. Definir o valor de correção de potência, se necessário. Este parâmetro é descrito no capítulo 6.5.4.
18. Certifique-se de que uma almofada isoladora na mesa de trabalho ou na divisória feita de folha de alumínio está limpa - não pode estar suja nem mecanicamente danificada no local onde o elétrodo é pressionado contra o material soldado.
ATENÇÃO! A almofada isoladora deve ser colocada diretamente sob o material soldado, uma vez que se destina a proteger o operador contra um arco elétrico formado entre o elétrodo de soldadura e a mesa de trabalho.
ATENÇÃO! Se a divisória tiver sido coberta com a almofada isolante, esta deve aderir firmemente à mesa - de modo a que não se encontrem impurezas entre a divisória e a mesa de trabalho.
Atenção! Evitar colocar qualquer coisa sob o elétrodo de terra. Se, durante o processo de soldadura, for necessário colocar o material a soldar sob o elétrodo de terra, a camada sob o elétrodo de terra deve ser tão fina quanto possível.
19. Descer a pinça com o elétrodo utilizando a alavanca de pé. Observar se a mensagem aparece na janela principal do painel HMI informando que o elétrodo atingiu a posição inferior.
20. Premir simultaneamente os dois botões START quando o elétrodo for pressionado contra o material. Mantenha os botões START premidos até à contagem decrescente dos parâmetros de soldadura definidos na receita. Soltar os botões durante o ciclo pára o ciclo.
ATENÇÃO: Para ligar a solda de alta frequência, ambos os botões START nas estações de controlo devem ser premidos simultaneamente. Utilizar as duas mãos para efetuar esta operação. No modo manual, é necessário premir e não largar os botões durante todo o tempo de soldadura. São estritamente proibidas quaisquer outras acções que evitem premir os botões com as duas mãos.
ATENÇÃO: o processo de soldadura na máquina é indicado na coluna de sinalização luminosa (luz laranja).
ATENÇÃO: Durante o tempo de soldadura, é estritamente proibido aproximar-se da pinça, do elétrodo ou do guia de ondas e tocar-lhes com as partes do corpo ou objectos metálicos, devido ao risco de queimaduras eléctricas, inflamação do arco elétrico ou poluição das ferramentas.
ATENÇÃO: o botão de PARAGEM DE EMERGÊNCIA foi concebido para ser premido em qualquer altura, especialmente quando a paragem de emergência é imediatamente necessária.
21. Observar as indicações apresentadas no amperímetro. CORRENTE DO ANÓIDE - a corrente da placa deve subir na faixa da área verde indicada na tabela do amperímetro.
22. Utilizar a alavanca de pé para puxar o elétrodo para cima e verificar a qualidade da soldadura.
23. Verificar a suavidade da soldadura.
24. Dependendo do resultado da primeira soldadura (soldada, não soldada, sobreaquecida), ajustar adequadamente os parâmetros de soldadura:
- POTÊNCIA INICIAL
- POTÊNCIA DE FUNCIONAMENTO
- TEMPO DE ATRASO
- TEMPO DE SOLDADURA
- TEMPO DE ARREFECIMENTO
- PRESSÃO (ajustar manualmente)
- POWER LEVEL (ajustar manualmente)
- MODO DE CORRENTE
- REGULAÇÃO DO CONDENSADOR
- CORRECÇÃO DE POTÊNCIA.
25. A máquina deve ser submetida a muitas horas de testes. Deve ser testada quando o produto é repetível. É altamente recomendável verificar o ciclo de trabalho da máquina, a sua funcionalidade e ergonomia na linha de produção.
26. Depois de receber um resultado de soldadura satisfatório em termos de resistência e estética visual, escrever os parâmetros de soldadura como uma receita: HMI → Ecrã principal → botão Guardar receita → Janela da base de dados das receitas → introduzir o novo nome da receita na coluna NOME→ botão de seleção
. A nova receita aparece na lista de receitas.
6.9 Ciclo de trabalho e deveres do operador

1. Arrancar a máquina de acordo com o procedimento descrito no Capítulo 6.7.



- Potência inicial;
- Potência de funcionamento;
- Tempo de atraso;
- Tempo de soldadura;
- Tempo de arrefecimento
- Nível de potência




ATENÇÃO: , É possível parar o processo de AF utilizando o botão STOP na estação de controlo em qualquer altura.
ATENÇÃO: Para ligar a solda HF, ambos os botões START nas estações de controlo devem ser premidos simultaneamente. Utilizar as duas mãos para efetuar esta operação. No modo automático, não é necessário manter os botões premidos durante toda a duração do ciclo. No ciclo automático, os botões são utilizados apenas para iniciar o processo de soldadura. Qualquer outra ação que não seja a de premir os botões com as duas mãos é estritamente proibida.
ATENÇÃO: o processo de soldadura na máquina é indicado na coluna de sinalização luminosa (luz laranja).
ATENÇÃO: Durante a soldadura, é estritamente proibido tocar na pinça, no elétrodo, na guia de ondas com as partes do corpo ou objectos metálicos, devido ao risco de queimaduras eléctricas, inflamação do arco elétrico ou destruição das ferramentas.

Para além da potência de saída, da força de pressão e da posição paralela dos eléctrodos, outro aspeto de grande importância para o processo de soldadura é o tipo de material de base espalhado no rolo aterrado por baixo da película. Evite soldar sem a camada de material de base - a utilização de material de base reduz o risco de choques eléctricos. O material de base deve ter uma baixa taxa de perda dieléctrica. Podem ser, por exemplo, folhas de vidro epóxi, politetrafluoroetileno (Teflon), poliéster (MYLAR), folhas Presspan, Resotex, baquelite, etc. A espessura e a dureza do material de base dependem da espessura da película soldada. Normalmente, deve ser utilizado um material de base mais fino para películas mais espessas e um material de base mais espesso para películas mais finas. A espessura do material de base pode variar entre 0,1 e 1,5 [mm] e deve ser selecionada para um determinado tipo de película e condições de soldadura no decurso de várias experiências.
ATENÇÃO: A soldadura sem primário deve ser evitada. A utilização de um suporte adequado reduz o número de sobretensões no elétrodo.
7.2. SELECÇÃO DA POTÊNCIA INICIAL
Para obter o melhor desempenho possível e um número reduzido de rejeições, ajuste a potência para cada elétrodo utilizando o interrutor POWER LEVEL. O primeiro elemento permite o ajuste da alimentação do gerador, enquanto o segundo permite o ajuste da potência fornecida ao elétrodo e emitida para o material soldado. O ajuste da potência deve ser efectuado no decurso de várias experiências (de acordo com as instruções dadas pelo fabricante).
Quando se aumenta a potência de saída, observar o amperímetro que mede a corrente do ânodo. Se esta aumentar, significa que o processo de soldadura está a ser iniciado.
O tempo de soldadura deve ser definido para um valor tal que a alta frequência seja desligada quando o ponteiro do amperímetro parar. Verificar a qualidade da soldadura. Se a qualidade for insuficiente, aumentar a potência de saída e, se isso não ajudar, aumentar o tempo de soldadura. Não definir uma potência de saída demasiado elevada - pode levar a danos nos produtos ou mesmo no material de base e nos eléctrodos.
Deve assumir-se como regra que, no caso da soldadura de PVC duro, o tempo de soldadura não deve exceder 4 - 5 segundos. As experiências mostraram que um tempo de soldadura mais longo, que exceda o intervalo acima mencionado, praticamente não tem qualquer impacto na qualidade da soldadura, mas reduz significativamente a eficiência do processo. Se as experiências realizadas mostrarem que a operação de soldadura demora mais de oito segundos, isso indica apenas uma seleção inadequada de um gerador para a carga ou a instalação do elétrodo de uma superfície demasiado grande. Depois de a tensão ter sido cortada dos eléctrodos, os materiais soldados devem arrefecer sob a unidade de prensagem. Se o elétrodo for levantado demasiado cedo, quando o material ainda é moldável, o material soldado é arrefecido de forma inadequada e deforma-se. A influência positiva do elétrodo no processo de arrefecimento é fácil de compreender se percebermos que, embora o elétrodo pareça estar muito quente, a sua temperatura é ainda muito inferior à temperatura da película soldada. Como resultado, o elétrodo pode absorver o calor da película soldada e arrefecê-la rapidamente.
Por conseguinte, é necessário deixar o material soldado arrefecer sob a unidade de prensagem durante 0,52 segundos. O tempo de arrefecimento deve ser selecionado no decurso de várias experiências, tendo em conta que um tempo de arrefecimento demasiado longo implica perdas desnecessárias de tempo de produção
A soldadura de películas de PVC macio requer a pressão dos eléctrodos contra o material soldado. A medição da pressão óptima dos eléctrodos pode ser difícil e essas medições não são realmente necessárias na prática. Para ajustar a pressão adequada, é geralmente suficiente discernir os casos de soldadura incorrecta e o aspeto da soldadura incorrecta, que podem indicar um ajuste inadequado da pressão. Uma pressão demasiado baixa pode ser indicada pelos seguintes sintomas:
- suscetibilidade de ocorrência de descargas de faíscas entre dois eléctrodos, uma vez que o ar, que deveria ter sido espremido, se encontra entre duas camadas de folha metálica, formando assim uma intensidade de corrente irregular;
- ocorrência de bolhas de ar na costura;
- o aspeto da resistência da costura que é pequena
Se a pressão for particularmente baixa, pode ocorrer algo normalmente designado por "ebulição da película". Quando a película é soldada sob pressão muito baixa, pode ser deformada num produto espumoso de resistência muito baixa. A aplicação de uma pressão excessiva também é inadequada, uma vez que pode tornar a película muito fina ao longo do local de soldadura e, assim, resultar também numa menor resistência do material soldado. Por conseguinte, recomenda-se que se siga o princípio de que a espessura da película após a soldadura deve ser igual a, pelo menos, metade da espessura inicial de ambas as camadas da película. O aparecimento e a forma correcta da fuga caraterística que normalmente se forma ao longo de ambos os bordos do local soldado tem também uma influência significativa nas propriedades de resistência do material soldado. Se essa fuga não aparecer, normalmente indica uma resistência insuficiente do local soldado, que pode ser facilmente testada. A ausência de fuga após o processo de soldadura pode ser causada pela aplicação de uma potência de saída demasiado baixa ou de uma pressão insuficiente. Se utilizar eléctrodos com arestas de corte, é muito importante posicionar corretamente a aresta de corte. Normalmente, assume-se que a aresta de corte do elétrodo deve sobressair do plano de soldadura cerca de metade da espessura da película soldada. Para verificar o funcionamento da aresta de corte, é necessário efetuar vários ciclos de soldadura de teste e remover os restos de película. O resultado dos ensaios pode ser considerado satisfatório quando a remoção dos restos de película ao longo da linha de soldadura não requer mais do que um corte com uma tesoura.
8.0 Manutenção
Devido às soluções de construção aplicadas e à estrutura descomplicada da máquina, as actividades de manutenção e controlo, tanto preventivas como de emergência, são relativamente simples e não requerem longas pausas no funcionamento da máquina.
A máquina de soldar requer uma pequena quantidade de trabalho relacionado com o funcionamento e a manutenção da máquina, desde que sejam mantidas as condições de utilização adequadas. É necessário verificar regularmente o estado técnico da ligação da máquina à rede eléctrica, nomeadamente o estado do sistema de proteção contra choques eléctricos.
Todos os componentes do gerador de alta frequência, nomeadamente todos os elementos isolantes, devem ser mantidos limpos. O interior do sistema de saída do gerador deve ser cuidadosamente limpo pelo menos uma vez de três em três meses. Após esta limpeza, deve verificar-se o estado dos componentes do gerador e das unidades que cooperam diretamente com o gerador e todas as ligações devem ser apertadas.
Devido às características específicas da máquina, recomenda-se que algumas das tarefas acima mencionadas sejam efectuadas por pessoal de assistência técnica autorizado e devidamente qualificado do Fabricante (isto aplica-se particularmente a situações de emergência). As tarefas acima mencionadas requerem cuidados e atenção especiais.
ATENÇÃO: Durante o funcionamento do gerador, os seus componentes, bem como os componentes do circuito de saída, têm uma tensão até 8 kV DC e uma tensão de alta frequência até 220 V (27,12 MHz ).
ATENÇÃO: Os condensadores do gerador de ânodo podem manter a carga eléctrica da tensão até 8000 VDC mesmo depois de a máquina de soldar ser desligada da fonte de alimentação. Antes de tocar nos componentes do gerador de alta-frequência, estes condensadores devem ser sempre descarregados.
A ligação à terra da estrutura da máquina deve ser efectuada com especial cuidado. Lembrar que o gerador nunca deve funcionar com as telas de proteção removidas, mesmo durante as actividades de assistência técnica e manutenção, quando o nível de segurança da máquina pode ser inferior devido à reparação em curso.
Todas as tarefas de manutenção e reparação requerem uma autorização das pessoas autorizadas.
Deve manter um REGISTO DA MÁQUINAincluindo as datas e os tipos de actividades preventivas ou reparações efectuadas.
Durante as tarefas de manutenção ou quaisquer outras operações manuais necessárias, nunca entrar ou colocar quaisquer partes do corpo na área exposta a perigos potenciais e previsíveis, a fim de eliminar o risco de situações perigosas potenciais e previsíveis.
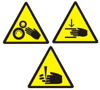
Usar sempre vestuário de proteção e calçado antiderrapante, reduzindo o risco de queda. Assegurar sempre que as mangas estão bem apertadas à volta dos pulsos ou devidamente enroladas.
Utilizar sempre luvas de trabalho quando se trabalha com componentes com arestas vivas.
Todo o pessoal responsável pela operação e manutenção da máquina deve ser devidamente formado e instruído.
Toda e qualquer operação de manutenção ou reparação só pode ser efectuada por pessoal autorizado e qualificado, capaz de interpretar corretamente os defeitos e as falhas, de ler os esquemas de instalação e os desenhos técnicos, de modo a garantir que todas as operações de desmontagem e montagem relacionadas com os procedimentos de manutenção normalizados sejam efectuadas de forma profissional e - o que é mais importante - segura.
Todas as tarefas realizadas na área de funcionamento da unidade de prensagem, ou seja, a montagem e desmontagem do elétrodo, realizadas quando a alimentação eléctrica da máquina está ligada, podem ser realizadas exclusivamente pelo pessoal devidamente formado em Saúde e Segurança no Trabalho, incluindo particularmente o risco envolvido no funcionamento da unidade de prensagem.
Deve também prever o potencial comportamento não normalizado da máquina, quando o sistema pneumático da máquina de soldar ou as condutas de fornecimento de ar comprimido não estão selados. Isto resultará numa descida automática lenta da unidade de prensagem da máquina de soldar.
O pessoal deve ser informado sobre esse risco durante a formação em saúde e segurança no trabalho.
ATENÇÃO: Durante todas e cada uma das operações acima mencionadas, o funcionamento da máquina deve ser interrompido.
8.2 Programa Preventivo - Controlos Periódicos
NO INÍCIO DE CADA TURNO
- Verificar se a zona de utilização da máquina está limpa e arrumada;
- Verificar visualmente se os ecrãs de proteção estão bloqueados;
- Verificar a iluminação da zona de trabalho;
- Verificar se o botão de PARAGEM DE EMERGÊNCIA funciona corretamente;
- Verificar a proteção principal na instalação eléctrica;
- Verificar o estado dos elementos condutores de cobre e latão na área do suporte do elétrodo e dos elementos de ligação à terra dos ecrãs de proteção laterais.
A CADA 100 HORAS DE FUNCIONAMENTO DA MÁQUINA (PELO MENOS UMA VEZ POR SEMANA):
- Verificar se os parafusos de suporte de carga (incluindo, em especial, os parafusos que fixam as ferramentas) estão corretamente fixados e apertados;
- Verificar o nível de água de condensação no recipiente do filtro de ar comprimido; se houver água, esvaziar o recipiente; se houver grandes quantidades de contaminantes sólidos, desmontar e lavar o recipiente;
A CADA 500 HORAS DE FUNCIONAMENTO DA MÁQUINA (MAS PELO MENOS DE DUAS EM DUAS SEMANAS)
- Verificar se o radiador da lâmpada de ânodo está limpo;
- Verificar a quantidade de contaminantes sólidos e de poeiras na câmara do gerador; se for necessário, limpar a câmara com um aspirador ou uma pistola de ar comprimido;
- Verificar se os elementos móveis (nomeadamente as ferramentas e as guias) estão limpos;
- Lubrificar os elementos móveis, nomeadamente as guias; se necessário, utilizar massa sólida à base de lítio e um lubrificador;
- Verificar e testar a unidade de alarme.
A CADA 1000 HORAS DE FUNCIONAMENTO DA MÁQUINA (MAS PELO MENOS DE SEIS EM SEIS MESES)
- Verificar visualmente o estado dos elementos mecânicos;
- Apertar todos os parafusos;
- Verificar se as medidas de proteção contra choques eléctricos funcionam corretamente;
- Verificar a eficácia da lubrificação das guias;
- Verificar o estado dos elementos de contacto principais - os contactores principais ou outros elementos de contacto do sistema, tais como contactores ou relés com superfícies excessivamente desgastadas, devem ser substituídos.
ATENÇÃO: Antes de cada manutenção, desligar a máquina utilizando o interrutor principal e desligar a alimentação eléctrica.
ATENÇÃO: Antes de cada manutenção, desligar a máquina utilizando o interrutor principal e desligar a alimentação eléctrica.
Os elementos mais importantes utilizados na máquina, utilizados para elevar e garantir a segurança do seu funcionamento são:
- detectores de caixa aberta
- interrutor de PARAGEM DE EMERGÊNCIA facilmente acessível, situado no painel de controlo, que desliga a máquina em qualquer altura
- um conjunto de sensores e detectores que verificam o funcionamento correto da máquina e dos seus sistemas individuais, ligados à sinalização no painel do operador
- salvaguardas adicionais no algoritmo de controlo da máquina que impedem o arranque da máquina em situações potencialmente perigosas
- A própria estrutura da máquina garante a máxima segurança do seu funcionamento.
9.1 Requisitos básicos
As questões relacionadas com a segurança e saúde no trabalho e a avaliação dos riscos durante o contacto de uma pessoa com a máquina foram descritas em pormenor nos capítulos anteriores deste manual. Como esta questão é extremamente importante, algumas instruções são repetidas nesta secção.- A máquina pode ser utilizada exclusivamente de forma adequada ao seu objetivo explicitamente descrito no ponto 1.
- As soluções construtivas aplicadas relacionadas com a segurança reduzem ao mínimo tanto o comportamento atípico da máquina como os riscos para os operadores e outras pessoas que tenham contacto com a máquina, desde que sejam respeitados os princípios de trabalho seguro. A máquina está equipada com interruptores de chave nos ecrãs de proteção e botão de PARAGEM DE EMERGÊNCIA.
- Todos os novos trabalhadores que tenham contacto com a máquina de soldar devem receber formação no domínio dos princípios básicos de saúde e segurança no trabalho e familiarizar-se com os tipos de riscos envolvidos no funcionamento da máquina de soldar, a menos que o operador siga os regulamentos e princípios obrigatórios.
- O pessoal responsável pela operação da máquina de soldar deve ter conhecimentos profundos de primeiros socorros em caso de choques eléctricos e queimaduras. No caso de pessoas que trabalhem com aparelhos que utilizem ondas electromagnéticas de frequência compreendida entre 0,1 e 300 MHz, são necessários exames médicos periódicos.
- Após a instalação da máquina de soldar, é necessário medir a emissão do campo eletromagnético e definir os limites da zona perigosa.
- ATENÇÃO: a lâmpada contém metais de terras raras e óxidos de metais de terras raras que são altamente tóxicos. Em caso de quebra, a lâmpada deve ser eliminada com o máximo cuidado e com a ajuda de serviços especializados
- Com base nos resultados das medições, o nível de perigo e o tempo durante o qual os operadores podem permanecer na zona de perigo são determinados de acordo com as normas aplicáveis.
- Só podem entrar na zona perigosa os operadores que tenham as aprovações adequadas para trabalhar na área exposta ao campo eletromagnético, com base em exames médicos especializados, e que tenham recebido formação adequada para o funcionamento seguro dos dispositivos que emitem campos electromagnéticos
- As medições acima mencionadas devem ser efectuadas por uma instituição autorizada. As instruções pormenorizadas relativas a tais medições são especificadas pelos regulamentos aplicáveis no país onde a máquina é utilizada.
- O Destinatário do aparelho assume toda a responsabilidade jurídica e financeira por eventuais ocorrências resultantes do desconhecimento desta documentação ou do incumprimento das regras de segurança. A leitura e o cumprimento das suas indicações são ABSOLUTAMENTE OBRIGATÓRIOS
- Com base nas informações contidas nesta documentação e no conhecimento da sua própria tecnologia de produto, o Destinatário é obrigado a desenvolver um MANUAL DE TRABALHO para os funcionários que operam esta máquina.
- Antes de iniciar qualquer trabalho na máquina, cada operador deve ler o conteúdo desta documentação e ter um MANUAL DE ESTACIONAMENTO preparado.
- Os operadores de máquinas devem usar sempre vestuário de trabalho normalizado, luvas, capacetes e calçado antiderrapante.
- O ambiente de trabalho da máquina, o chão e os suportes e pegas manuais devem estar sempre limpos e isentos de qualquer contaminação, gordura ou lama, a fim de reduzir ao mínimo possível o risco de escorregamento ou queda.
- Nunca utilizar a máquina no modo de funcionamento automático sem os elementos de proteção fixos ou móveis. Verificar regularmente se todos os interruptores de emergência e todos os outros elementos de proteção estão bem montados e se funcionam corretamente.
- Todos os operadores da máquina devem ser instruídos sobre as funções dos elementos de proteção da máquina e a sua utilização correcta.
- Na área circundante da máquina (cerca de 1,5 m à volta da máquina), não pode haver objectos que possam interferir com o funcionamento da máquina. Esta zona deve ser mantida limpa e ter uma iluminação adequada.
- Nunca utilizar os manipuladores da máquina ou os tubos flexíveis como suportes. Lembre-se de que qualquer movimento acidental do manipulador da máquina pode acidentalmente iniciar o funcionamento da máquina.
- Informe sempre o supervisor e/ou o pessoal de trânsito sobre todo e qualquer caso de funcionamento incorreto da máquina.
- Todas as tarefas de manutenção e reparação requerem uma autorização das pessoas autorizadas.
- Deve manter um Registo da máquinaincluindo as datas e os tipos de actividades preventivas ou reparações efectuadas.
- Durante as tarefas de manutenção ou quaisquer outras operações manuais necessárias, nunca entrar ou colocar quaisquer partes do corpo na área exposta a perigos potenciais e previsíveis, a fim de eliminar o risco de situações perigosas potenciais e previsíveis.
NUNCA UTILIZAR A MÁQUINA DE SOLDAR QUANDO AS TELAS DE PROTECÇÃO ESTIVEREM REMOVIDAS OU QUANDO OS INTERRUPTORES DE CHAVE ESTIVEREM BLOQUEADOS. ISTO APLICA-SE PARTICULARMENTE AOS PAINÉIS DE PROTECÇÃO DO GERADOR. Estes painéis de proteção reduzem a emissão de campos electromagnéticos e impedem o contacto acidental com os elementos do circuito elétrico com tensão de alimentação ou alta tensão até 8000 V.
- Usar sempre vestuário de proteção e calçado antiderrapante, reduzindo o risco de queda. Assegurar-se sempre de que as mangas estão bem apertadas à volta dos pulsos ou devidamente enroladas.
- Utilizar sempre luvas de trabalho quando se trabalha com componentes quentes ou com arestas vivas.
- Deve-se também lembrar que nos componentes que não foram cobertos por uma proteção por razões ergonómicas, ou seja, o elétrodo e os componentes condutores do suporte do elétrodo, existe tensão de alta frequência. NUNCA TOCAR NESSES COMPONENTES DURANTE O PROCESSO DE SOLDADURA.
- O contacto com estes componentes durante o processo de soldadura provoca queimaduras na pele devido à tensão de alta frequência. No entanto, não é perigoso para a vida ou para a saúde.
- O método adotado de alimentação eléctrica da máquina de soldar apresenta um risco potencial de prensagem ou esmagamento de membros no espaço entre a prensagem dos eléctrodos. Todo e qualquer trabalho na área de operação da unidade de prensagem, ou seja, montagem e desmontagem de eléctrodos ou espalhamento e remoção de material e sucata, que é realizado quando a máquina de soldar está ligada à alimentação eléctrica, pode ser feito exclusivamente por funcionários com formação na área da saúde e segurança no trabalho, incluindo a informação sobre o risco colocado pela unidade de prensagem.
- Durante o funcionamento da máquina, o operador deve estar na área indicada abaixo
Área de trabalho do ZD-NX-4 (cor verde)
9.3 Condições de segurança no trabalho do pessoal responsável pela manutenção e reparação da máquina de soldar- Todas as tarefas de manutenção e reparação requerem uma autorização das pessoas autorizadas.
- É PROIBIDO efetuar qualquer trabalho de assistência, manutenção ou prevenção sem desligar a máquina da alimentação eléctrica. Estes trabalhos requerem cuidados especiais. É preciso ter sempre presente que os condensadores do gerador de ânodo podem reter cargas eléctricas com uma tensão de 5000 V mesmo depois de a máquina de soldar ter sido desligada da rede de alimentação. Antes de tocar nos componentes do gerador de alta frequência, estes condensadores devem ser sempre descarregados.
- É PROIBIDO lubrificar a máquina durante o funcionamento.
- Todo o pessoal responsável pela operação e manutenção da máquina deve ser devidamente formado e instruído.
- Durante o funcionamento do gerador, os seus componentes, bem como os componentes do circuito de saída, têm a tensão de alta frequência. A ligação à terra da estrutura da máquina deve ser efectuada com especial cuidado. É preciso também lembrar que o tempo de funcionamento do gerador com os escudos de proteção removidos deve ser reduzido ao mínimo.
- Todas as reparações devem ser efectuadas de acordo com os princípios vigentes de reparação e funcionamento dos aparelhos por uma pessoa que possua um certificado adequado emitido pela associação de electricistas competente (na Polónia: SEP).
- Toda e qualquer operação de manutenção ou reparação pode ser efectuada exclusivamente por pessoal autorizado e qualificado, capaz de interpretar corretamente os defeitos e as falhas e de ler os esquemas de instalação, de modo a garantir que todas as operações de desmontagem e montagem relacionadas com os procedimentos de manutenção normalizados sejam efectuadas de forma profissional e - o que é mais importante - segura.
- Durante as tarefas de manutenção ou quaisquer outras operações manuais necessárias, nunca entrar ou colocar quaisquer partes do corpo na área exposta a perigos potenciais e previsíveis, a fim de eliminar o risco de situações perigosas potenciais e previsíveis.
- utilização da máquina de qualquer outra forma que não a descrita neste Manual de Operação e Manutenção
- instalação incorrecta, não realizada de acordo com os procedimentos descritos neste manual
- operação inadequada da máquina ou operação por pessoal sem formação adequada
- fornecimento de parâmetros inadequados à máquina
- manutenção insuficiente da máquina
- alterações ou interferências não autorizadas por pessoas sem as licenças, autorizações ou formação necessárias,
- utilização de peças sobresselentes que não sejam de origem
- quaisquer acções de qualquer pessoa que não estejam de acordo com os princípios especificados neste Manual de Operação e Manutenção e quaisquer informações de aviso.
10.0 Documentação eléctrica
10.1 Parâmetros da fonte de alimentação - Dados técnicos
Alimentação eléctrica |
3 x 220 VAC; 50/60 Hz |
Proteção da cabeça |
40 A |
Capacidade instalada |
6 kVA |
Potência de saída HF |
4 kW |
Tensão de funcionamento |
24 VDC |
Frequência de funcionamento |
27,12 MHz |
Estabilidade da frequência |
+/- 0.6 % |
Lâmpada geradora (tríodo metal-cerâmica) |
7T85RB |
Sistema de circuito anti-descarga |
ANTIFLASH completo com filtro HF |
10.2 Lista de dispositivos eléctricos
Todos os componentes utilizados na máquina são componentes eléctricos típicos disponíveis em qualquer loja especializada. O fabricante, ao selecionar estes elementos, em caso de substituição, deixa a escolha ao destinatário, desde que os substitutos utilizados tenham os mesmos parâmetros técnicos. A lista dos aparelhos eléctricos consta do capítulo 13.3. Se tiver alguma dúvida, contacte o fabricante.
10.3 Desenhos de conceção da instalação eléctrica
NOTA: O esquema elétrico está incluído no apêndice deste manual.
Ver Apêndice
11.0 Documentação pneumática
11.1 Dados técnicos
Pressão de funcionamento |
0,4 - 0,8 MPa |
Consumo de ar comprimido |
Máx. 11 nl (standard) por ciclo |
Pureza do ar |
de acordo com a norma ISO8573-1:4-4-4 |
Desempenho da filtragem |
20 um (ISO8573-1 4-4-4) |
O sistema pneumático da máquina de soldar desempenha a sua função:
- unidade de prensagem

VER APÊNDICES
12.0 Instruções gerais
12.1 Instruções gerais
As soluções de construção aplicadas e os componentes de alta qualidade permitem o funcionamento correto da máquina durante um período de cerca de 30 anos. No entanto, podem ocorrer algumas alterações nas necessidades do utilizador final ou alterações nos princípios ou normas que não podem ser previstas atualmente, o que pode exigir a eliminação da máquina antes do fim do período acima mencionado. O mesmo se aplica às peças ou componentes substituídos ou reparados da máquina de soldar.
O Utilizador Final é obrigado a garantir que a eliminação da máquina ou dos seus componentes é efectuada de acordo com os requisitos legais aplicáveis num determinado momento e num determinado local.
Todos os componentes da máquina são recicláveis. A eliminação de resíduos perigosos deve ser sempre efectuada por empresas especializadas.
Os tipos de resíduos produzidos durante o ciclo de vida da máquina são descritos no ponto 12.2
12.2 Resíduos
Todos os resíduos produzidos no decurso de actividades de substituição ou de assistência técnica, contaminados com gordura, não podem ser eliminados juntamente com os resíduos industriais.- resíduos líquidos ou sólidos de gorduras
- massa lubrificante remanescente após a lubrificação ou manutenção da máquina
- pedaços de pano ou de papel saturados com substâncias utilizadas para a limpeza dos componentes da máquina
- peças sobressalentes usadas da máquina, consoante o material de que são feitas
- lâmpada do gerador!!!.
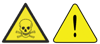
Todos os resíduos produzidos no decurso de actividades de substituição ou de assistência técnica, que estejam contaminados com gordura, não podem ser eliminados juntamente com os resíduos industriais. Todos os resíduos gerados durante o processo de produção devem ser separados e armazenados em locais designados e marcados.

12.3 Procedimento de desmontagem da máquina antes da eliminação
-
- Posicionar a máquina de modo a que fique imóvel.
- Desligar a alimentação eléctrica da máquina.
- Desligar a alimentação de ar comprimido da máquina.
- Remover as condutas flexíveis de plástico ou borracha e assegurar a sua eliminação por uma empresa especializada.
- Desligar e retirar os fios e dispositivos eléctricos e assegurar a sua eliminação por uma empresa especializada.
- Separar os componentes de aço e os componentes de metais não ferrosos e assegurar a sua eliminação por uma empresa especializada.
13.0 Apêndices
13.1 Etiqueta do modelo e do número de série
Cada máquina Miller Weldmaster tem este autocolante localizado na parte de trás da máquina. Identifica o modelo e o número de série de cada máquina de soldar.
Indicará também a tensão e os hertz necessários para o funcionamento.
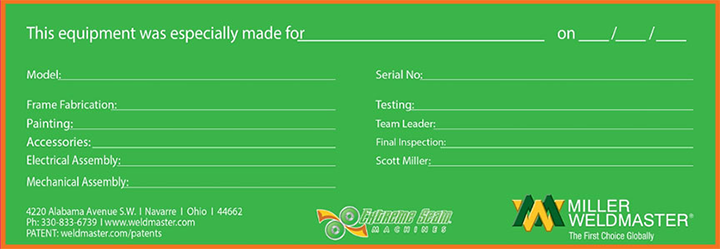